Welding 4.0 – ewm Xnet welding management system
A step towards more efficient and resource-saving welding technology
Why ewm Xnet?
Intelligent and productivity-boosting networking of man and machine for an automatic flow of data within the production chain: Industry 4.0 is now becoming established in welding production thanks to the new and innovative ewm Xnet Welding 4.0 welding management system.
-
Quality assurance and improvement – improved quality is the greatest asset
- Documentation of welding parameters and welders of every run for long-term records of weld quality
- WPS linked to component, on-time monitoring of parameters directly on the welding machine and clear assignment of required welder qualifications all reduce errors
- Mandatory specifications from component management and WPS manager ensure that the correct parameters are always set
- Xbutton ensures expert welding and supports welding coordination personnel by identifying welder qualifications
-
Increased productivity
Increased productivity – complete more work in the same time
- Longer arc times per shift improve efficiency
- Paperless transfer of all relevant data and WPS directly to the workplace reduce non-productive time
- Preset welding parameters reduce the number of error corrections
- Fewer unnecessary downtimes thanks to prompt, consumption-oriented maintenance notes, for e.g. consumables
-
Cost reduction – increased profits with the same turnover
- Consumption values for power, gas and welding consumables are recorded to recognise potential savings
- Prompt maintenance instructions instead of early warnings lead to a minimised consumption of wear parts
- Transparent processes ensure constructive controlling with the option of precise final costing
Cost reduction
Needs-based depending on requirements
The ewm Xnet system modules and components
Customised for the requirements of specialist production – EWM’s Welding 4.0 welding management system also adheres to this philosophy of needs-based products. The three interrelated ewm Xnet modules adjust to any individual requirements depending on the type and size of the company. The update capability typical of EWM products is also integrated: Additional modules can be retrofitted easily at any time. ewm Xnet provides measurable benefits from the first module onwards no matter which version you decide to purchase.
The ewm Xnet modules
✔ Platform-independent – browser-based for all end devices ✔ Comprehensively extendable – room for improvement ✔ LAN/WiFi control connection – wireless network
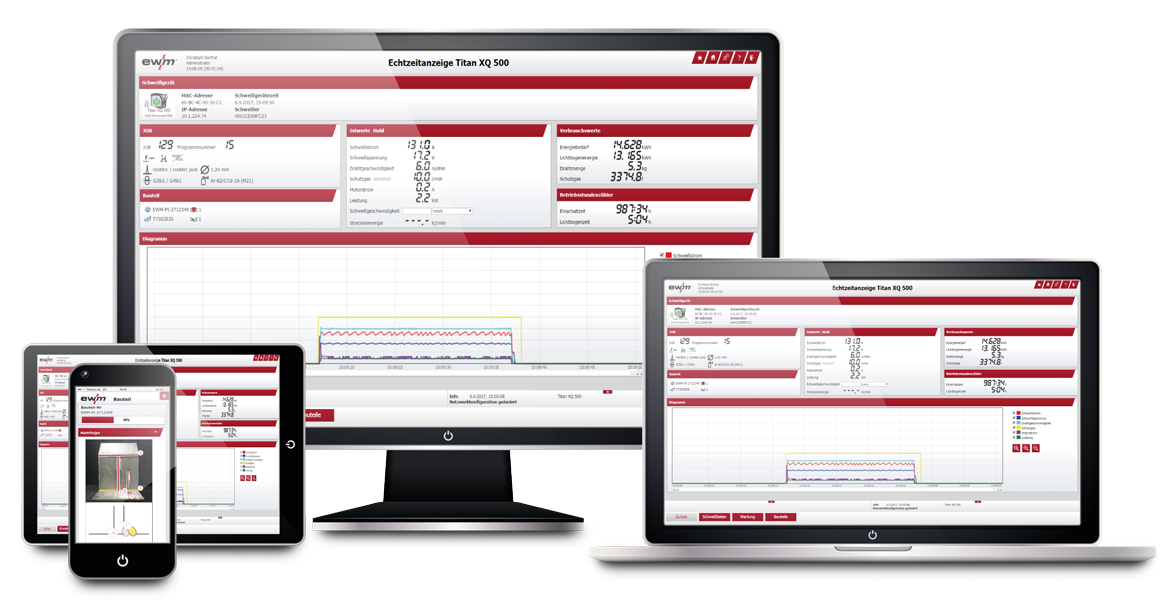
Plug & Play Set
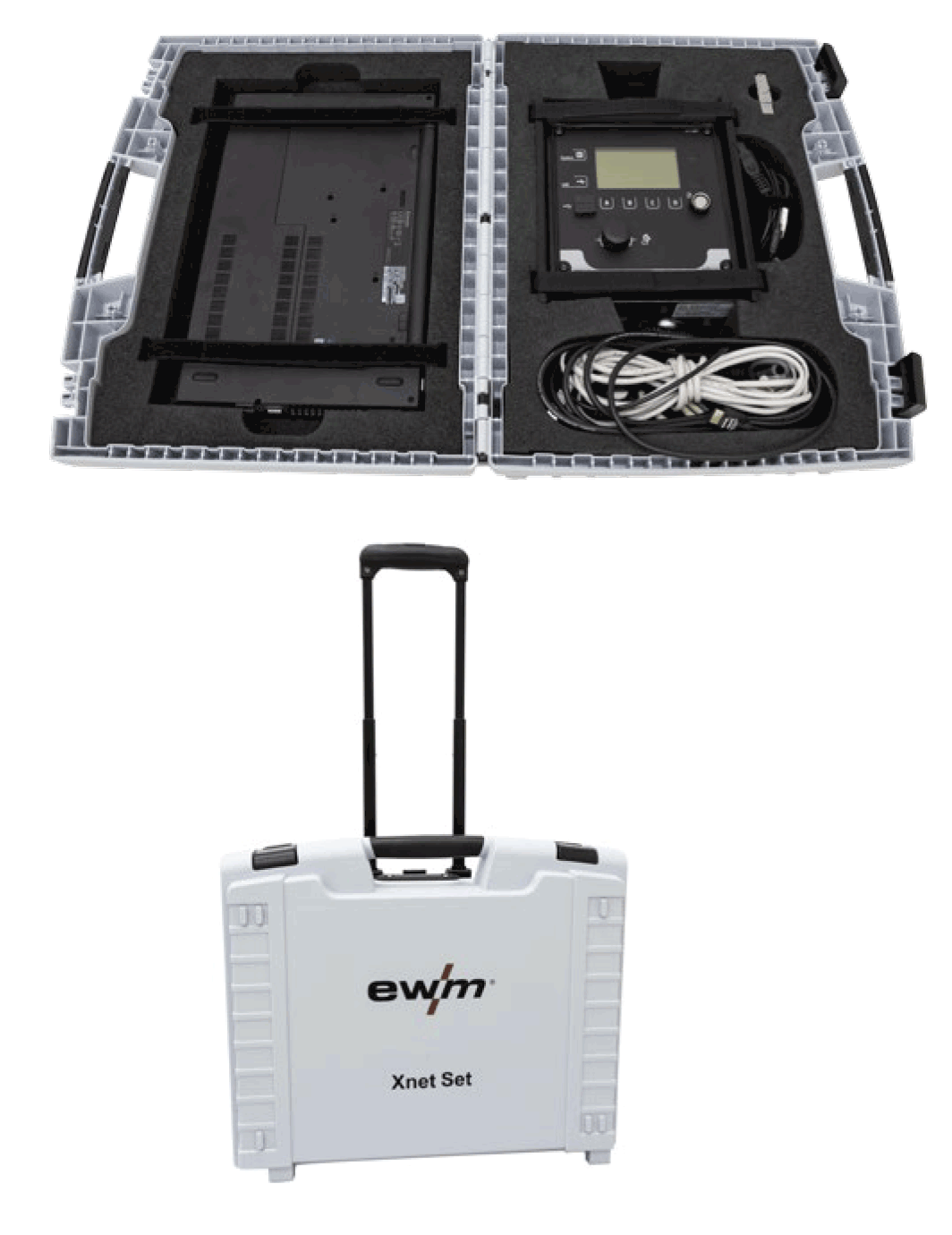
YOUR BENEFITS
The ewm Xnet Plug and Play Set facilitates smooth and simple commissioning and usage. It is the perfect solution for rapid, order-based documentation of welding parameters with a power source. With the ewm Xnet Basis Set already installed, welding data can be recorded and an efficiency analysis generated. With the pre-configured PC and gateway, the system can be connected in just a few steps via plug and play. The prerequisite is a welding machine with a 7-pole interface without hard-coded ewm Xnet components.
CONTENTS
- Laptop PC with pre-installed ewm Xnet software (ewm Xnet Basis Set)
- USB dongle with software usage licence, 1 machine usage licence, ewm Xnet Basis Set
- ewm Xnet LAN gateway
- Cables (7-pole, LAN network)
- Plastic case with Trolly
Universal logger
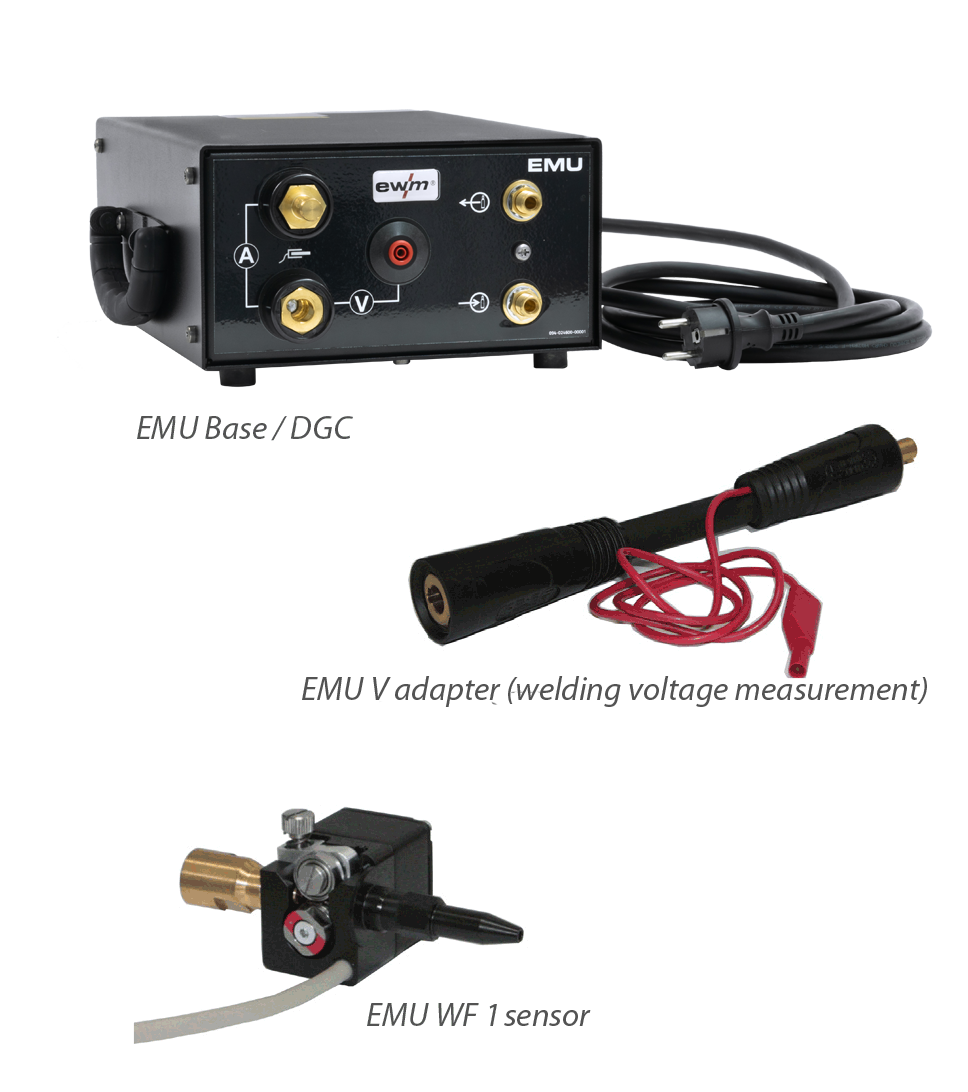
YOUR BENEFITS
- With the ewm Xnet Universal logger, welding machines from all manufacturers can be connected to an ewm Xnet gateway and the ewm Xnet software.
- This means you can use almost all ewm Xnet functions, such as:
- Real-time display, recording and documentation of the welding parameters
- Consumption calculation
- Welding machine maintenance
- Bar code scanning
- WPQ Manager
- Welder management
- Two different options are available for recording the wire feed speed of the connected welding machine:
- Mathematical calculation of the wire feed speed based on the measured welding current without an additional EMU WF 1 sensor wire sensor
- Metrological recording of the wire feed speed using the EMU WF 1 sensor wire sensor
Overview of functions
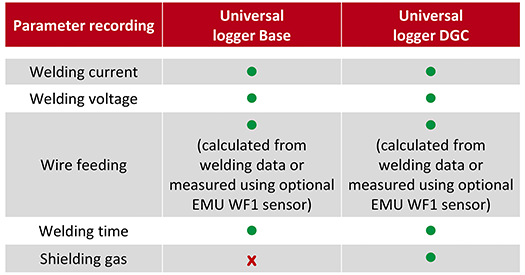
Fields of application
- Suitable for the following machines:
- MIG/MAG welding machines
- TIG welding machines
- Plasma welding machines
- MMA/electrode welding machines
- Submerged arc welding machines (on request)
- For applications in:
- Welding production
- Training centres
- Manual/mechanised/automated welding
- Service centres
- Welding machine leasing
- Data recording during welding procedure tests and welder examinations
ewm Xnet documents for download
Welding 4.0 – ewm Xnet welding management system brochure
ewm Xnet Universal logger brochure
ewm Xnet scope of services and functions
ewm Xnet form for error messages
ewm Xnet Factsheet