Safety information on HF ignition
Information on dealing with the high-frequency ignition on TIG power sources
Contents
1. Introduction
- Electric current
- Arc radiation
- Thermal energy
- Hazardous substances
- Noise
It is especially important not to underestimate the danger posed by electric currents. Therefore, it is essential to handle them correctly and employ protective measures during welding. Protective measures can only be taken correctly if the endangered person fully understands the nature of the hazard. Use of technically sound power sources is essential.
The following aims to illustrate the dangers of electric currents and the protective measures that must be taken. The focus of this document is on the use of the high‐frequency (HF) start function required for TIG welding. Explaining how the HF start works shall provide safety officers with the knowledge required to make a well‐founded assessment.
2. Electrical hazards and their effect on the body
The German Social Accident Insurance (Deutsche Gesetzliche Unfallversicherung, DGUV) describes the danger of electric currents as being hard to recognise, because it can’t be heard, smelt or seen. The DGUV 209‐010 information document titled “Lichtbogenschweißen” (arc welding) lists electrical hazards, among others. It states that an electrical hazard begins when:
- The voltage is higher than 25 V alternating voltage (root‐mean‐square value) or 60 V direct voltage
- And a sufficiently strong current is able to flow.
The effect of electricity on a person is determined by the extent of the electric resistance in the person. Electricity can only flow in a closed circuit. The interrelationship is described by Ohm’s law with voltage (U) in volts (V), current (I) in amperes (A) and the extent of the resistance (R) in ohms (Ω):
It can be deduced from this that increasing the resistance causes the flow of electric current to decrease. Therefore, the goal is to maximise the resistance between the person and the hazard areas using insulators. The level of resistance differs depending on which part of the body comes into contact with the electric circuit, and thus closes it.
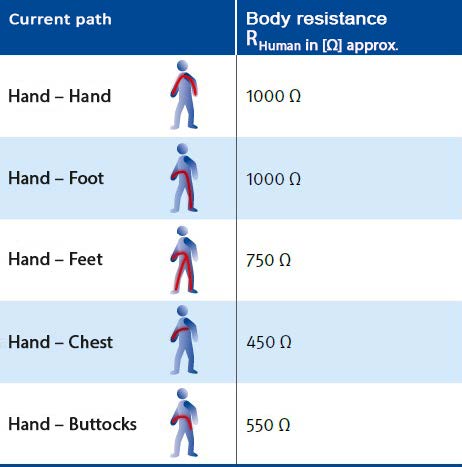
Electric shocks can have various effects on the body, including muscle cramping, shock and ventricular fibrillation. Aside from the voltage, the strength of the current also depends largely on the resistances in the electric circuit. As well as the resistance provided by the body, protective clothing must be taken into consideration here. The most important thing is to maintain sufficient distance from the hazard in order to achieve the greatest possible insulation from the welding circuit. The person must never form part of the electric circuit.
3. Technical classification and description of a high-frequency start
3.1 General introduction
Welding machines are designed to convert the available mains current into the form desired or required to carry out a welding task. Modern inverter machines are capable of modelling direct or alternating current in various forms.
direct current, welding power sources are subject to the 2014/35/EU Low Voltage Directive. This defines in general terms how machines must be introduced to the market to ensure that they do not pose a threat to personal safety.
Furthermore, there are other standards that build on the Low Voltage Directive to establish rules for specific product groups. Welding power sources are subject to the very extensive DIN EN IEC 60974 standard. This comprehensively lays out a set of demands on safety and performance that must be observed. As well as electric safety measures, the standard defines other measures such as protection against heating.
In principle, standards regarding the assessment of hazards to the body are based on healthy people. Whilst limit values are not arbitrary, values lower than limit values should not be generalised as being safe.
The permissible voltage can be either the working voltage or the open circuit voltage. The working voltage is present when the arc is burning, usually with a voltage of 10–40 V. Conversely, the open circuit voltage is present between the connection points when no arc is burning. This is higher than the working voltage, as higher voltages are required to ignite the arc.
Part 1 of the DIN EN IEC 60974 (Arc welding equipment – Part 1: Welding power sources), defines the maximum voltage needed to make welding tasks possible without putting the welder at an unnecessarily high risk. DGUV 209‐010 categorises these values by operating condition, as shown in the following table:
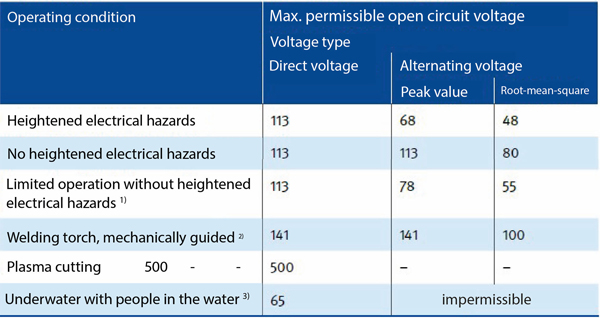
EWM power sources are generally designed to allow all limit values to be reached while operating the machine in the presence of heightened electrical hazards.
A special arc ignition device is required when using contactless ignition in TIG welding. This creates an arc ignition voltage that superimposes the open circuit voltage and far exceeds it.
3.2 Arc ignition devices on TIG power sources
The air gap between the tungsten electrode tip and the workpiece acts as an insulator. The high‐frequency start function works when a high enough voltage is applied that allows to overcome the insulator. In electrical engineering, this voltage is also known as breakdown voltage and is dependent on various factors, such as the material or the gas. Using argon as a shielding gas makes ignition easier because it ionises more easily.
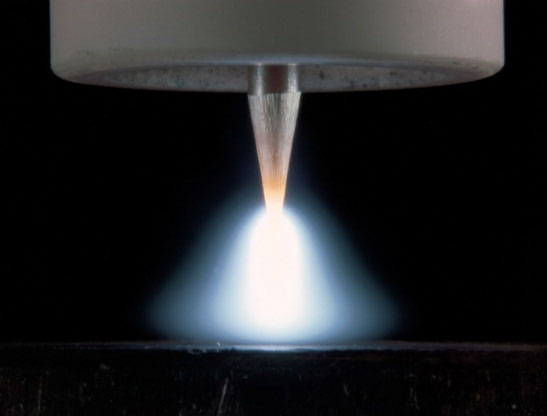
Special regulations are set out in DIN EN IEC 60974‐3 (VDE 0544‐3) for arc ignition devices. In Part 1, it states that superimposed arc ignition voltages may exceed the abovementioned open circuit voltages (11.1.5).
A high‐frequency start for TIG welding is always a current pulse with a very high voltage. The rated value for this peak voltage (Up) is limited to a maximum of 15 kV for manually operated welding torches and added to the open circuit voltage (U0):
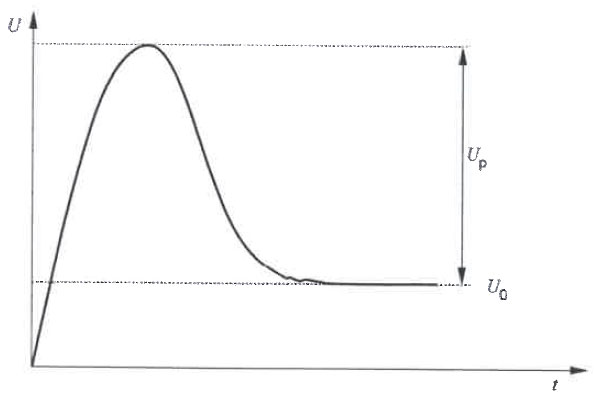
Chapter 11.2 of DIN EN 60974-3 explicitly mentions the danger of pulse current. It may cause an electric shock when the following two conditions are met:
- The human body is in direct contact with the output of the arc ignition device.
- The human body is in series with the arc path, thus forming part of the welding circuit.
In practice, the second condition listed is especially dangerous for the welder, and occurs in the absence of sufficient insulation between the body and the welding circuit. Therefore, it must always be ensured that the welder does not form part of the circuit. This finding is fundamentally important for the prevention of electric shocks and must be implemented using various measures (see chapter 4). The person can form part of the circuit by touching the workpiece, or simply by means of earthing:
3.3 Rules and limit values of an ignition device
In order to minimise the dangers posed by mishandling this high voltage, the maximum moderate energy is restricted, along with other limit values. This is also stipulated by DIN EN IEC 60974-3. According to the standard, the key value of 4 joules may not be exceeded within 1 second (manually operated welding torches).
Other limit values are also important. The height, duration and frequency of the pulses are restricted as follows:
- The maximum amplitude is 15 kV.
- The maximum charge of a current pulse is 8 μC. This produces a pulse length of 1 μs.
- The maximum energy within 1 second is 4 J. This limits the frequency of the pulses to around 100 per second.
DIN EN 60335‐2‐76 (VDE0700) can be consulted for a better assessment of the abovementioned values. The standard also defines specific requirements for pasture fences. The fence helps herd the animals by sending a pulsed flow of extremely short electrical pulses through the animal’s body. The circuit remains open until it is closed by the animal when it acts as a connection between the fence and the ground (return circuit).
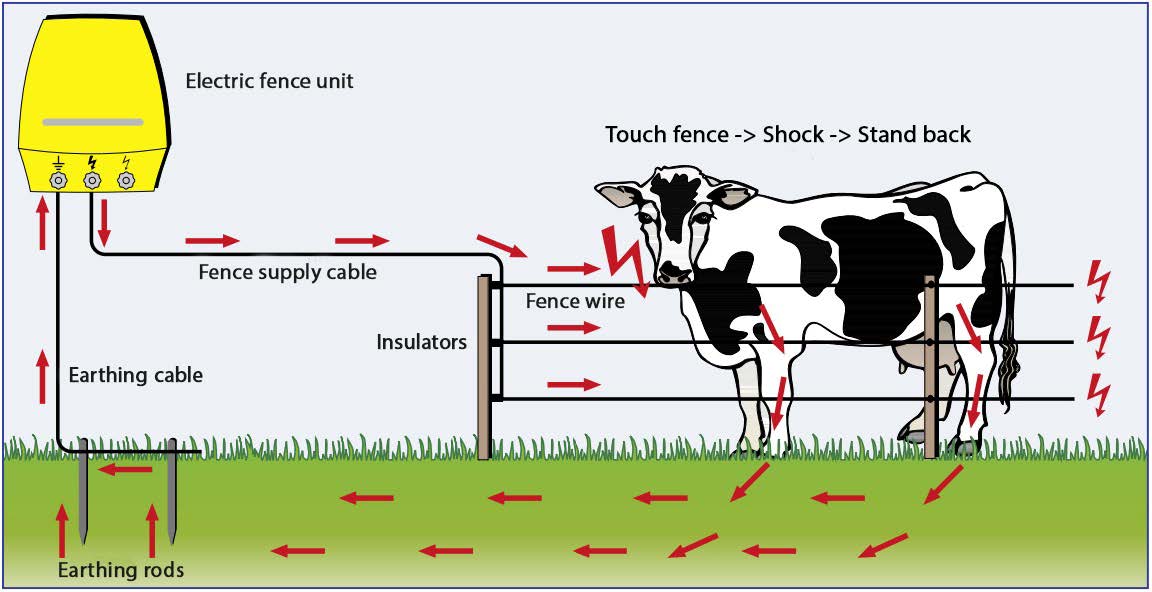
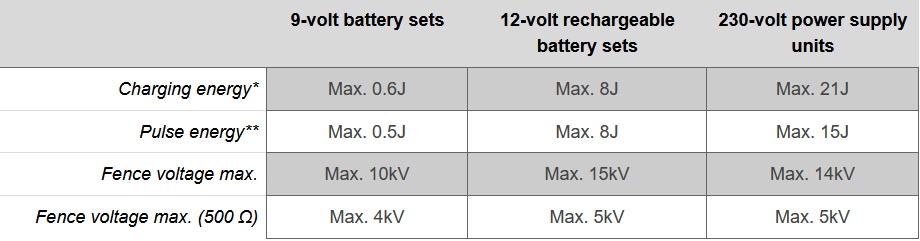
The maximum permissible voltages exceed the values stated in the DIN EN 60674-3 standard on welding power sources, especially in the case of 230‐V power supply units.
4. Necessary protective measures for safe operation of TIG power sources
As previously described in paragraph 2, the danger posed to a human by an electric current depends largely on the resistance within the circuit. For that reason, insulating the welder from the circuit is the top priority in terms of protection. DGUV 209‐010 states that, as well as clothing and protective equipment, the ambient conditions play a major role (chapter 4.1.5.). Since not every part of the welding circuit can be protected against direct contact, other protective measures are required. These must include the following as a minimum:
- Clothing that provides as much insulation as possible. Even exposure to perspiration can reduce the resistance offered by clothing. Small conductive parts (e.g. buttons, fasteners) can also reduce the protective effect.
- Safety shoes with rubber soles
- Leather gloves designed for welding (dry, undamaged, DIN EN 12477‐compliant)
- Insulating mat
It is the person’s own responsibility to behave properly to ensure that they do not form part of the circuit. The measures outlined above only supplement this behaviour, and will have no effect in the case of improper behaviour.
There is a common misconception that simple insulators provide sufficient protection on their own. Since an HF start involves penetrating an insulator (the air gap between the welding torch and the workpiece), the protection must involve a number of different measures. To better illustrate this, the following shows some examples of how a highfrequency start can even break through insulators in the presence of reasonable measures:
It is clear that high‐frequency should only be used when combined with several protective measures. A grip and dry leather gloves are the first protective measures that can be taken. Distance, insulating mats and protective clothing are also necessary.
Improperly repaired welding torches, for example using insulating tape, are a safety risk (see image above). Insufficient distance between the person and the workpiece is also dangerous, especially without protective clothing, as air has a dielectric strength of up to 0.35 kV/mm. This alone demands that a minimum distance be kept, even without taking into account other safety aspects.
Mistakes can happen in an instant, even when there is no initial indication that they might happen. There should also be sufficient insulation in objects such as seats to prevent the creation of conductive connections between the person and the workpiece. The insulation of the welder can also be threatened through use of additional materials in the form of long rods if care is not taken and these come into contact with surrounding objects. Propping objects up on the welding table can result in the clothing being the only source of insulation between the body and the workpiece. This means the insulation is much lower than in cases where the abovementioned protective measures are applied. Exposure to perspiration increases the conductivity of clothing.
Protective clothing and safety precautions are essential when dealing with switched-on power sources. Therefore, the power source must be switched off when changing the tungsten electrode or the gas nozzle. This welding process brings with it a slight possibility of accidental contact with the torch trigger, which would initiate the HF start.
In principle, EWM welding machines comply with all standards relating to open circuit voltage and the HF start. These are designed to minimise the risk to healthy individuals as much as possible (see chapter 3). Nonetheless, the risk of a high‐frequency start must not be underestimated. Therefore, it is absolutely necessary to teach appropriate personal behaviour by means of extensive instruction to exclude the risk of electric shock when combined with other protective measures.