Gefahrenhinweis HF-Zündung
Hinweise für den Umgang mit der Hochfrequenz-Zündung an WIG-Stromquellen
Inhaltsverzeichnis
1. Einleitung
- Elektrischer Strom
- Lichtbogenstrahlung
- Thermische Energie
- Gefahrstoffe
- Lärm
Insbesondere die Gefahr des elektrischen Stromes darf nicht unterschätzt werden. Daher ist der Einsatz von Schutzvorkehrungen während des Gebrauchs und der richtige Umgang notwendig. Nur wenn durch die gefährdeten Personen die Wirkungsweise der Gefahr verstanden wird, können Schutzmaßnahmen richtig umgesetzt werden. Der Einsatz von technisch einwandfreien Stromquellen wird dabei vorausgesetzt.
Im Folgenden soll auf die Gefahr des elektrischen Stromes hingewiesen und die erforderlichen Schutzmaßnahmen aufgezeigt werden. Dabei wird ein Fokus auf den Einsatz der für das WIG‐Schweißen notwendigen Hochfrequenzzündung liegen. Eine Beschreibung dieser soll helfen, verantwortlichen Sicherheitsfachkräften das notwendige Fachwissen für eine fundierte Einschätzung zu geben.
2. Elektrische Gefahren und deren Wirkungsweise im Körper
Die Deutsche Gesetzliche Unfallversicherung (DGUV) beschreibt die Gefahr des elektrischen Strom als eine schwer erkennbare Gefahr, da sie nicht hörbar, riechbar oder sehbar ist. In der DGUV Information 209‐010 „Lichtbogenschweißen“ werden u.a. die elektrischen Gefahren aufgezählt. Dabei wird davon ausgegangen, dass eine elektrische Gefährdung beginnt wenn:
- Die Spannung höher als 25V Wechselspannung (Effektivwert) oder 60V Gleichspannung beträgt
- Und dabei ein ausreichend hoher Strom fließen könnte.
Für die Wirkung des Stromes auf den Menschen ist von entscheidender Bedeutung, wie groß der elektrische Widerstandes im Menschen ist. So kann Strom nur in einem geschlossenen Stromkreis fließen, der Zusammenhang wird durch das ohmsche Gesetz beschrieben mit der Spannung (U) in Volt (V), der Stromstärke (I) in Ampere (A) und der Größe des Widerstandes (R) in Ohm (Ω):
Daraus ist zu erkennen, dass mit steigendem Widerstand der Stromfluss abnimmt. Ziel ist es daher, den Widerstand zwischen dem Menschen und den gefährdeten Bereichen durch Isolatoren so groß wie möglich zu gestalten. Je nachdem, welcher Teil des Körpers den Kontakt zum Stromkreis hat und damit diesen schließt, entstehen unterschiedliche Körperwiderstände.
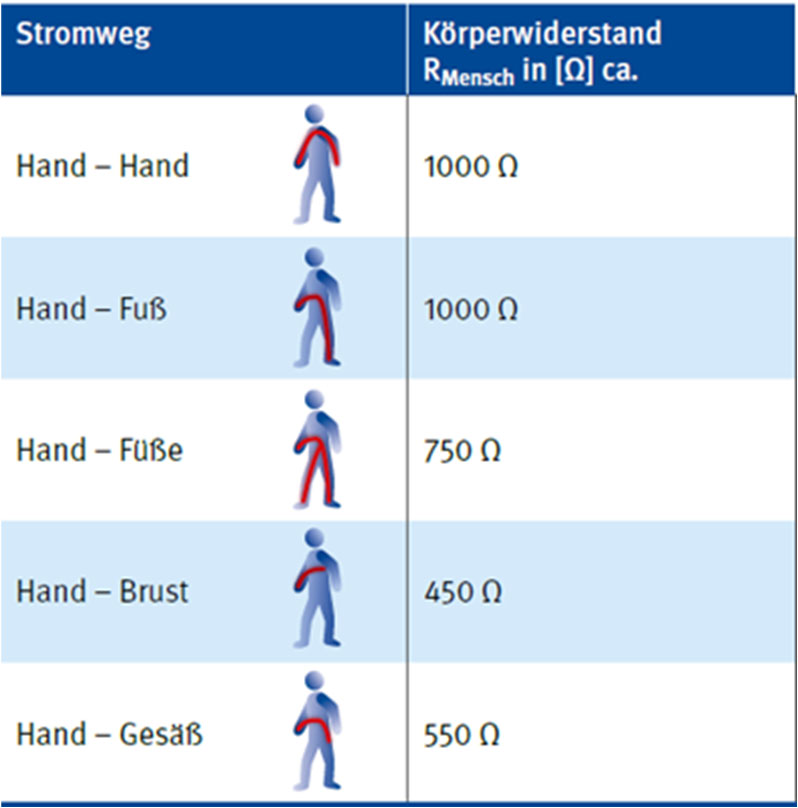
Körperdurchströmungen können unterschiedliche Auswirkungen haben, wie Muskelverkrampfung, Nervenerschütterung, Herzkammerflimmern und weitere. Dabei hängt die auftretende Stromstärke neben der Spannung auch maßgeblich von den Widerständen im Stromkreis ab. Daher ist nicht nur der Körperinnenwiderstand, sondern auch die Schutzkleidung zu betrachten. Dabei ist vorallem ein ausreichender Abstand einzuhalten, um eine möglichst große Isolierung vom Schweißstromkreis zu erreichen. Der Mensch darf niemals Teil des Stromkreises sein.
3. Technische Einordnung und Beschreibung einer Hochfrequenzzündung
3.1 Allgemeine Einleitung
Schweißgeräte haben die Aufgabe, den zur Verfügung stehenden Netzstrom so umzuwandeln, dass dieser in der notwendigen und gewünschten Form für eine Schweißaufgabe zur Verfügung steht. Dabei sind moderne Inverter Geräte in der Lage, Gleich‐ oder Wechselstrom in unterschiedlichen Arten und Formen zu modellieren.
Wie alle elektrischen Geräte, die mit Nennspannungen zwischen 50‐1000V Wechselstrom bzw. 75‐1500V Gleichstrom arbeiten, unterliegen auch Schweißstromquellen der Niederspannungsrichtlinie 2014/35/EU. Dabei wird allgemein definiert, wie Geräte in Verkehr gebracht werden müssen, damit diese die Sicherheit von Menschen nicht gefährden.
Darüber hinaus existieren weitere Normen die, aufbauend auf die Niederspannungsrichtlinie, Regeln für spezielle Produktgruppen aufstellen. Schweißstromquellen unterliegen der sehr umfangreichen DIN EN IEC 60974 und ihren Teilen. In dieser wird umfassend geregelt, welche Sicherheits‐ und Leistungsanforderungen zu erfüllen sind. Dabei werden nicht nur elektrische Sicherheitsvorkehrungen definiert, sondern auch weitere wie z.B. Schutzmaßnahmen gegen Erwärmung.
Grundsätzlich gehen Normen bezüglich der Einschätzung von Gefahren für den Körper von gesunden Menschen aus. Daher sind Werte unterhalb der Grenzwerte nicht pauschal als ungefährlich zu bezeichnen, allerdings werden Grenzwerte auch nicht willkürlich gewählt.
Bezüglich der erlaubten Spannungen wird zwischen Arbeits‐ und Leerlaufspannung unterschieden. Die Arbeitsspannung tritt auf, wenn der Lichtbogen brennt und liegt i.d.R. zwischen 10‐40V. Die Leerlaufspannung hingegen liegt zwischen den Anschlussstellen an, wenn kein Lichtbogen brennt. Diese ist höher als die Arbeitsspannung, da für die Zündung des Lichtbogens größere Spannungen notwendig sind.
In der DIN EN IEC 60974 Teil 1 (Lichtbogenschweißeinrichtungen – Teil 1: Schweißstromquellen) wird diese auf ein Maximum festgelegt, sodass Schweißaufgaben möglich sind, aber eine unnötig hohe Gefährdung ausgeschlossen ist. Die DGUV 209-010 fasst diese Werte je nach Einsatzbedingungen in folgender Tabelle zusammen:
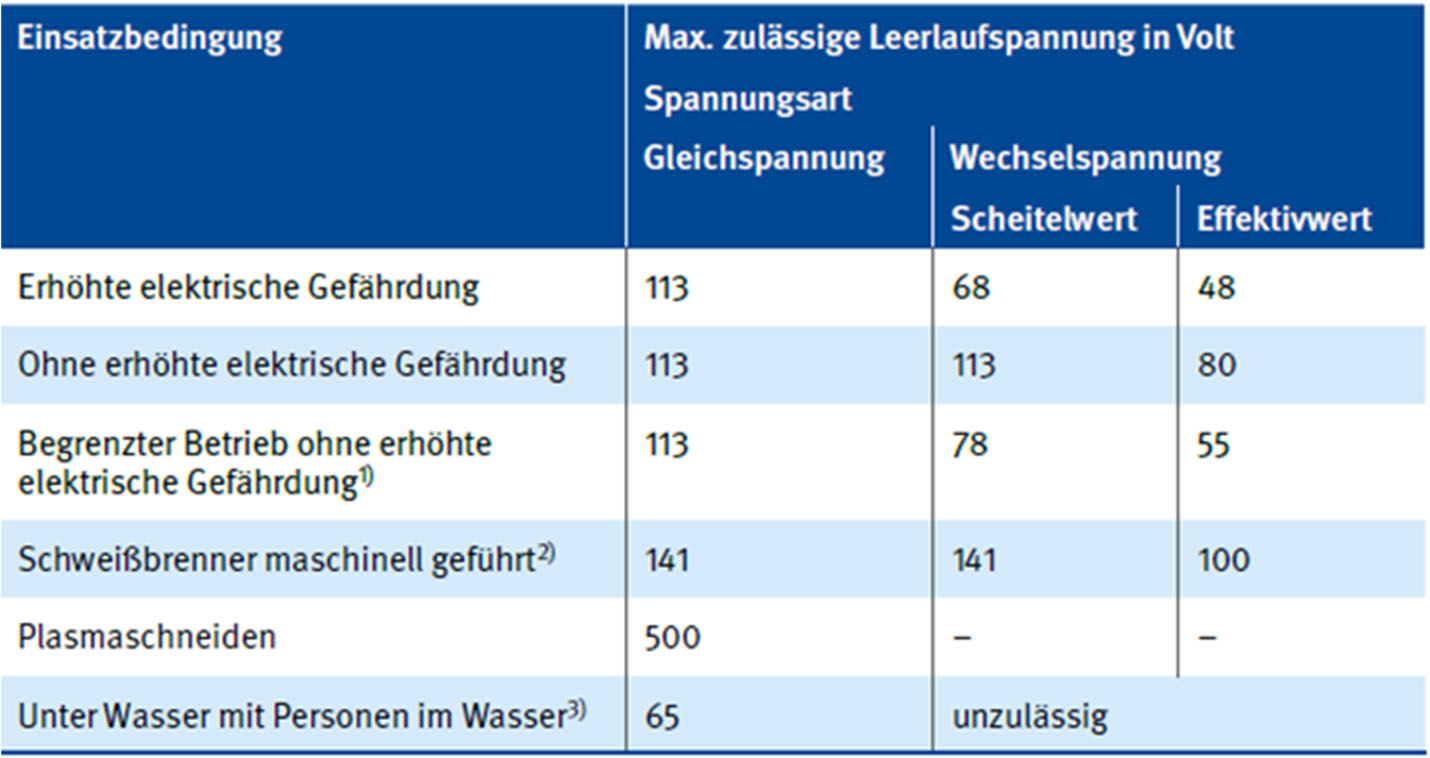
EWM Stromquellen werden grundsätzlich so ausgelegt, dass alle Grenzwerte für den Betrieb unter erhöhter elektrischer Gefährdung möglich ist.
Für das WIG‐Schweißen ist bei Einsatz der berührungslosen Zündung eine spezielle Lichtbogenzündeinrichtung notwendig. Diese erzeugt eine Lichtbogenzündspannung, welche die Leerlaufspannung überlagert und deutlich höher liegt als diese.
3.2 Lichtbogenzündeinrichtungen an WIG-Stromquellen
Die Luftstrecke zwischen Wolframelektrodenspitze und Werkstück fungiert als Isolator. Die Hochfrequenzzündung ist daher so konstruiert, dass sie durch Anlegen einer hohen Spannung diesen Isolator überwindet. In der Elektrotechnik wird diese Spannung auch Durchschlagspannung genannt. Diese hängt von unterschiedlichen Faktoren wie dem Material bzw. Gas ab. Argon als Schutzgas erleichtert die Zündung, da dieses leichter ionisiert.
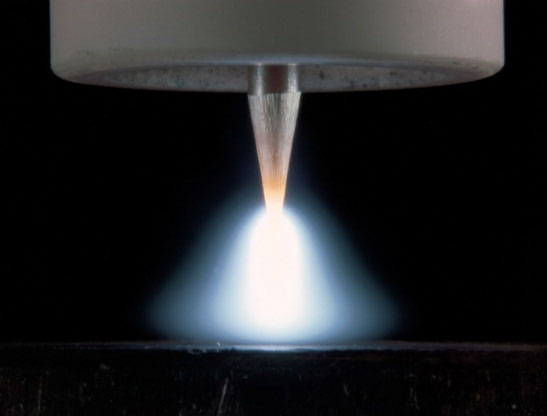
Lichtbogenzündeinrichtungen sind speziell in der DIN EN IEC 60974‐3 (VDE 0544‐3) geregelt. Dabei wird bereits in Teil 1 festgelegt, dass überlagerte Lichtbogenzündspannungen die o.g. Leerlaufspannungen überschreiten darf (11.1.5).
Eine Hochfrequenzzündung für das WIG‐Schweißen ist immer ein Stromimpuls mit sehr hoher Spannung. Der Bemessungswert für diese Scheitelspannung (Up) ist begrenzt, beträgt bei handgeführten Brennern maximal 15kV und wird auf die Leerlaufspannung (U0) addiert:
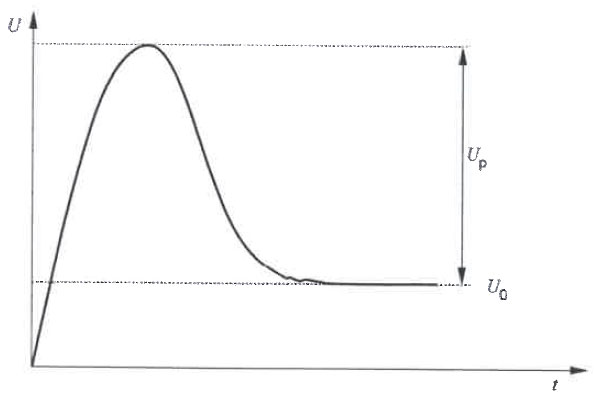
Im Kapitel 11.2 der DIN EN 60974‐3 wird explizit auf die Gefahr des Impulsstromes eingegangen. Dabei kann eine Gefährdung durch elektrischen Schlag aufgrund von zwei Bedingungen entstehen:
- Der menschliche Körper ist in direktem Kontakt mit dem Ausgang der Lichtbogenzündeinrichtung
- Der menschliche Körper ist elektrisch in Reihe mit der Lichtbogenstrecke als Teil des Schweißstromkreises
Insbesondere der letzt genannte Punkt ist in der Praxis eine besondere Gefahr für den Schweißer und ensteht bei nicht ausreichender Isolation zwischen Körper und Schweißstromkreis. Es ist daher immer darauf zu achten, dass der Schweißer nicht Teil des Stromkreises ist. Diese Erkenntnis ist elementar wichtig, um Stromschläge zu verhindern und muss durch unterschiedliche Maßnahmen (siehe Kap. 4) umgesetzt werden. Dabei kann der Mensch sowohl bei Berührung des Werkstückes, aber auch durch Erdung bereits Teil des Stromkreises sein:
3.3 Regeln und Grenzwerte einer Zündeinrichtung
Um die Gefahren durch diese Hochspannung bei falscher Handhabung zu minimieren, wird u.a. die maximale mittlere Energie begrenzt. Dies geschieht ebenfalls in der DIN EN IEC 60974‐3. Laut Norm darf innerhalb einer Sekunde der wichtige Wert von 4 Joule (handgeführte Brenner) nicht überschritten werden. Darüber hinaus sind weitere Grenzwerte wichtig.
Damit sind die Höhe, Dauer und Häufigkeit der Pulse wie folgt begrenzt:
- Die maximale Amplitude beträgt 15kV.
- Die maximale Ladung eines Stromimpulses darf 8μC nicht überschreiten. Daher ergibt sich die Pulslänge von 1μs.
- Die maximale Energie innerhalb einer Sekunde ist auf 4J begrenzt. Damit wird die Häufigkeit der Pulse pro Sekunde eingeschränkt (etwa 100 pro Sekunde).
Für eine bessere Einschätzung der oben genannten Werte, kann die DIN EN 60335‐2‐76 (VDE0700) dienen. In dieser werden besondere Anforderungen an Weidezäune definiert. Dabei beruht die Hütewirkung auf der impulsmäßigen Durchströmung des Tierkörpers mit extrem kurzzeitigen elektrischen Stromimpulsen. Der Stromkreis ist solange offen, bis das Tier diesen schließt, indem dieses die Verbindung zwischen Zaun und Boden herstellt (Rückleitung):
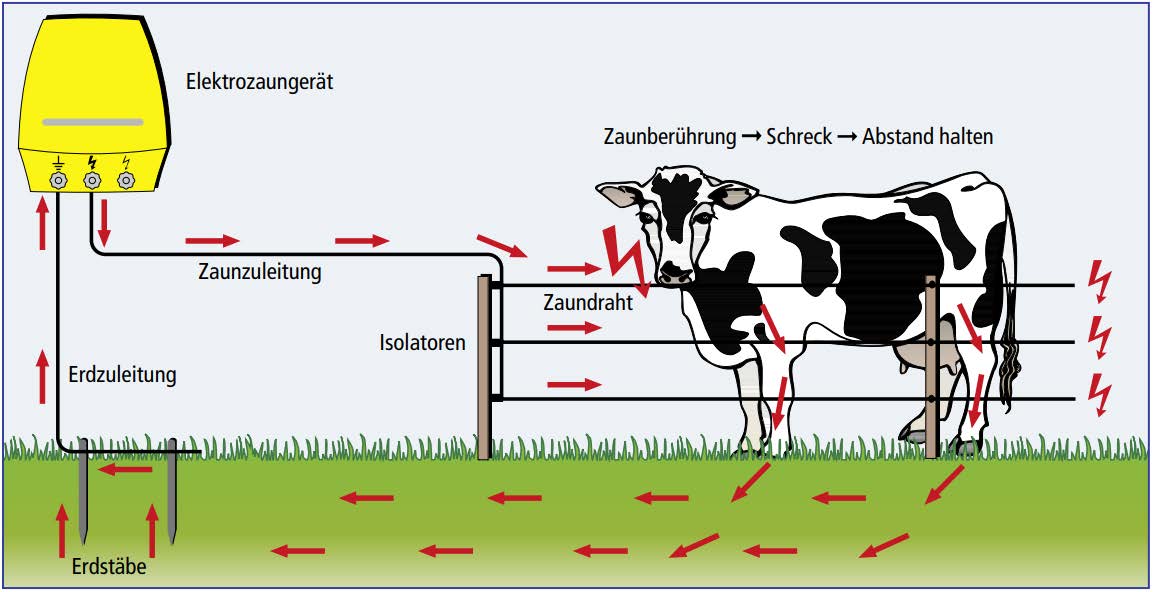
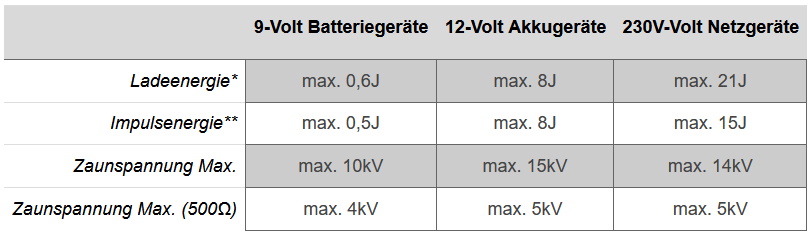
Die maximal zulässigen Energien übersteigen dabei insbesondere bei 230V‐Netzgeräten die in der für Schweißstromquellen relevanten Norm DIN EN 60674‐3 genannten Werte.
4. Erforderliche Schutzmaßnahmen für einen sicheren Betrieb von WIG-Stromquellen
Wie unter Absatz 2 bereits beschrieben, hängt der für den Menschen gefährliche Strom maßgeblich von den Widerständen im Stromkreis ab. Daher ist das oberste Schutzziel stets, den Schweißer vom Stromkreis zu isolieren. In der DGUV 209‐010 wird darauf hingewiesen, dass neben der Bekleidung und der Schutzaurüstung auch die Umgebungsbedingungen von Bedeutung sind (Kap.4.1.5.). Da nicht alle aktiven Teile des Schweißstromkreises gegen direktes Berühren geschützt werden können, sind zusätzliche Schutzmaßnahmen nötig, welche mindestens umfassen:
- Der Isolationswert der Kleidung sollte möglichst hoch sein, dabei kann z.B. verschwitze Kleidung bereits den Widerstand massiv herabsetzen – Wichtig ist auch, dass bereits kleine leitende Partien (z.B. Knöpfe, Nieten, etc..) die Schutzwirkung herabsetzen können.
- Sicherheitsschuhe mit Gummisohlen
- Handschuhe aus Leder, die für das Schweißen geeignet sind (trocken, unbeschädigt, nach DIN EN 12477)
- Isolierende Unterlage
Richtiges persönliches Verhalten ist die Notwendigkeit dafür, dass der Mensch nicht Teil des Stromkreises wird. Die oben beschriebene Maßnahmen unterstützen dies nur und sind bei unsachgemäßer Handhabung wirkungslos.
Eine häufige Fehlannahme ist, dass bereits einfache Isolatoren ausreichen, um einen wirksamen Schutz zu bieten. Da die Aufgabe einer HF‐Zündung darin liegt, einen Isolator (also die Luftstrecke zwischen Schweißbrenner und Werkstück) zu durchschlagen, müssen die Schutzmaßnahmen daher mehrere Einzelmaßnahmen umfassen. Für eine bessere Illustration sind im folgenden einige Beispiele gezeigt, wie die Hochfrequenzzündung bei günstigen Maßnahmen selbst vermeintliche Isolatoren durschlägt:
Es ist zu erkennen, dass die Hochfrequenz nur in Kombination mehrerer Schutzmaßnahmen wirkt. So ist die Griffschale bereits eine erste Schutzmaßnahme, gefolgt von trockenen Lederhandschuhen. Abstände, isolierende Unterlagen und Schutzkleidung sind ebenfalls notwendig.
Unsachgemäß reparierte Brenner mit z.B. Isolierband sind ein Sicherheitsrisiko (siehe Bild oben). Ein geringer Abstand der Person vom Werkstück, insbesondere ohne Schutzkleidung ist ebenfalls gefährlich, da Luft eine Durchschlagsfestigkeit von bis zu 0,35kV/mm besitzt. Damit ergeben sich bereits, ohne Sicherheitsfaktoren, Mindestabstände die eingehalten werden sollten.
Fehler können schnell passieren, auch wenn diese zunächst nicht offensichtlich sind. Es sollte z.B. auch die Sitzgelegenheit entsprechend isoliert sein, sodass keine leitfähige Verbindung zwischen Person und Werkstück entsteht. Auch die Verwendung von Zusatzmaterial in Form von Stäben kann bei größeren Längen dazu führen, dass diese bei Unachtsamkeit Kontakt mit der Umgebung haben und dadurch eine Isolation des Schweißers nicht mehr sichergestellt ist. Ein Aufstützen auf den Schweißtisch führt dazu, dass die Isolation zwischen Körper und Werkstück nur durch die Kleidung gegeben ist – damit ist diese deutlich geringer, als wenn die oben beschriebenen Schutzmaßnahmen eingehalten werden. Verschwitzte Kleidung erhöht die Leitfähigkeit dieser entsprechend.
Der Umgang mit einer eingeschalteten Stromquelle muss grundsätzlich mit Schutzkleidung und Sicherheitsmaßnahmen erfolgen. Daher ist z.B. für den Wechsel der Wolframelektrode oder der Gasdüse die Stromquelle auszuschalten. Ein versehentliches Berühren des Brennertaster ist während dieser Arbeiten leicht möglich und führt zum Einschalten der HF‐Zündung.
Grundsätzlich erfüllen EWM Schweißgeräte alle Normen bezüglich der Leerlaufspannung und der HF‐Zündung. Diese sind so ausgelegt, das das Risiko bei gesunden Menschen möglichst minimiert ist (siehe Kap. 3). Trotzdem darf ds Risiko der Hochfrequenzzündung nicht unterschätzt werden. Daher ist es absolut Notwendig, durch umfängliche Unterweisung ein richtiges persönliches Verhalten zu zeigen, dass in Zusammenspiel mit weiteren Schutzmaßnahmen das Risiko eines elektrischen Schlages von vornherein ausschließt.
Amortisationsrechner für unsere Schweißbrenner der PM/MT-Serie
Berechnen der Abkühlzeit t8/5
Der EWM Abkühlzeit-Rechner bietet Ihnen anhand einer einfachen und selbsterklärenden Menüführung einen starken Partner zur Berechnung der benötigten Abkühlzeiten und sorgt so für das gewünschte Schweißergebnis.
Schaefflerdiagramm
Mit unserem EWM-Schaeffler-Programm geben wir Ihnen ein leistungsstarkes Werkzeug an die Hand, mit dem Sie nach Auswahl oder Eingabe Ihrer Grundwerkstoffe und der zu erwartenden Aufmischung den richtigen EWM Schweißzusatzwerkstoff ermitteln können. Im Gefügeschaubild können Sie das zu erwartende Gefüge nach dem Schweißen ablesen.
Abgleich Leitungswiderstand
Der Leitungswiderstand wird für die neue Prozessregelung benötigt. Ohne diesen Abgleich ist bei Schlauchpaketlängen über 1,5m eine Korrektur der Lichtbogenspannung während des Schweißens nötig. Mit dem Abgleich des Leitungswiderstandes hingegen steht die Lichtbogenkorrektur selbst bei langen Leitungen nahezu bei 0 V.
Zudem ermöglicht dieser Abgleich die exakte Bestimmung und Anzeige der effektiven Lichtbogenleistung (kW), da deren Berechnung nicht länger durch die Verlustleistung der Schweißkabel verfälscht wird. Dadruch können Sie die benötigte Streckenenergie für die ideale Schweißnaht stets genau berechnen. Auch die Lichtbogenspannung wird nun korrekt angezeigt.
Videos
Welches Schutzgas beim WIG- und welches beim MIG/MAG-Schweißen?
WIG-Schutzgas
Wie aus dem Namen des Verfahrens schon abgeleitet werden kann, werden in der Regel inerte Gase zum WIG-Schweißen eingesetzt. Schutzgase sind in DIN EN 439 genormt. Diese tragen nach Norm die Bezeichnungen l1, l2 und l3.
Das am häufigsten beim WIG-Schweißen verwendete Schutzgas ist Argon (l1). Der Reinheitsgrad sollte mindestens 99,95% betragen. Bei Metallen, die eine sehr gute Wärmeleitfähigkeit haben, wie Aluminium oder Kupfer, kommt aber auch Helium (l2) zum Einsatz. Unter Helium als Schutzgas ist der Lichtbogen heißer. Vor allem aber ist die Wärmeverteilung zwischen dem Kern und dem Rand des Lichtbogens gleichmäßiger. Der Einsatz von reinem Helium beim WIG-Schweißen ist selten und auf Sonderfälle beschränkt, dagegen kommen Argon/Helium-Gemische (l3) mit 25, 50 oder 75% Helium seit einigen Jahren vermehrt zur Verwendung. Damit kann z.B. bei dickeren Aluminiumstrukturen die zur Erreichung eines ausreichenden Einbrandes erforderliche Vorwärmtemperatur verringert werden. Vielfach ist auch eine Erhöhung der Schweißgeschwindigkeit möglich. Beim WIG-Schweißen von nichtrostenden Chrom-Nickel-Stählen werden zu diesem Zweck auch Argon / Wasserstoffgemische (R1) eingesetzt, jedoch sollte der Wasserstoffgehalt aus Gründen der Porenvermeidung nicht wesentlich über 5% liegen.
Die Schutzgasdurchflußmenge richtet sich nach dem Gasdüsendurchmesser und der umgebenden Luftströmung. Als Richtwert kann bei Argon von einem Volumenstrom von 5-10 I / min ausgegangen werden. In zugigen Räumen Bild 4 sind u. U. größere Durchflußmengen erforderlich. Bei Argon / Helium-Gemischen müssen wegen der geringeren Dichte von Helium höhere Durchflußmengen eingestellt werden.
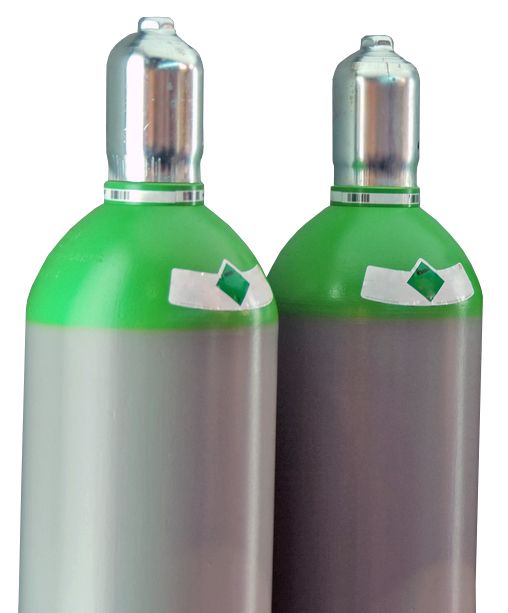
MIG/MAG-Schutzgas
Schutzgase zum MIG/MAG-Schweißen findet man in DIN EN 439. In dieser Norm sind alle Schutzgase zum Lichtbogenschweißen und -schneiden genormt. Die Schutzgase werden in sieben Gruppen und in weitere Untergruppen unterteilt.
Übersicht über die Gruppen der Schutzgase
Die Gruppe R
Die Gruppe R enthält Argon / Wasserstoff-Gemische, die eine reduzierende Wirkung haben. Die Gase der Gruppe R1 finden neben Argon und Helium Anwendung zum WIG-Schweißen und zum Plasmaschweißen, die Gase der Untergruppe 2 mit höherem Wasserstoffgehalt(H) dagegen zum Plasmaschneiden und zum Wurzelschutz (Formiergase).
Die Gruppe I
In der Gruppe I sind die inerten Gase zusammengefasst. Hier findet man Argon(Ar) und Helium (He) sowie Argon/Helium-Gemische. Sie werden zum WIG-, MIG-, und Plasmaschweißen eingesetzt, sowie auch zum Wurzelschutz.
Die Gruppe M
In der großen M-Gruppe, die noch in M1,M2 und M3 unterteilt ist, sind die Mischgase zum MAG-Schweißen zusammengefasst. Auch hier gibt es in jeder Gruppe noch 3 bzw. 4 Untergruppen. Die Gase sind von M1.1 bis M3.3 nach Ihrem Oxidationsverhalten geordnet, d.h. M1.1 verhält sich schwach oxidierend, M3.3 ist am stärksten oxidierend. Hauptbestandteil dieser Gase ist Argon, an aktiven Komponenten sind Sauerstoff (O) oder Kohlendioxid (CO2) bzw. Sauerstoff und Kohlendioxid (Dreikomponenten-Gase) zugemischt.
Die Gruppe C
In der Reihe der Gase zum MAG-Schweißen folgt in der Gruppe C das reine Kohlendioxid und ein Kohlendioxid /Sauerstoffgemisch. Letzteres hat allerdings in Deutschland keine Bedeutung. Die Gase der Gruppe C sind am stärksten oxidierend, weil das CO2 bei der hohen Temperatur des Lichtbogens zerfällt, wobei neben Kohlenmonoxid auch große Mengen Sauerstoff entstehen.
Die Gruppe F
In der Gruppe F findet man schließlich Stickstoff (N) und ein Stickstoff / Wasserstoff-Gemisch. Beide Gase können zum Plasmaschneiden und zum Formieren verwendet werden.
Neben dem Oxidationsverhalten verändern sich mit der Zusammensetzung des Gases auch die elektrischen und die physikalischen Eigenschaften im Lichtbogenraum und damit die Schweißeigenschaften. Durch den Zusatz von Helium zum Argon verbessert sich z.B. die Wärmeleitfähigkeit und der Wärmeinhalt der Lichtbogenatmosphäre. Beides führt zu einem energiereicheren Lichtbogen und damit zu einem besseren Einbrandverhalten. Das Zumischen von aktiven Komponenten bei den Mischgasen führt u.a. zu einer feineren Tropfenbildung beim Abschmelzen der Drahtelektrode. Ferner wird der Wärmetransport im Lichtbogen verbessert. Auch hieraus resultiert ein besseres Einbrandverhalten.
Die benötigte Durchflussmenge des Schutzgases lässt sich mit einer Faustregel errechnen, und zwar soll sie 10 - 12 x Drahtdurchmesser in Liter/Minute sein.
Beim MIG-Schweißen von Aluminium werden, wegen der großen Oxidationsneigung des Werkstoffs, etwas darüberhinausgehende Durchflussmengen eingestellt, bei Ar / He- Mischgasen, wegen der geringen Dichte von Helium, auch wesentlich höhere. Das aus der Flasche oder der Ringleitung kommende Gas wird zunächst im Druck reduziert. Die eingestellte Durchflussmenge kann an einem Manometer, das zusammen mit einer Staudüse geeicht ist, abgelesen werden, oder an einem Durchflussmengenmesser mit Schwebekörper.
Bezeichnung |
Angaben in Volumenprozent (Vol %) |
Übliche |
Bemerkungen |
||||||
Gruppe |
Kennzahl |
oxidierend |
inert |
reduziert |
reaktionsträge |
|
|
||
|
|
CO2 |
O2 |
Ar |
He |
H2 |
N2 |
||
R |
1 |
|
|
Rest² |
|
> 0 bis 15 |
|
WIG, Plasmaschweißen, Plasmaschneiden, Wurzelschutz |
|
2 |
|
|
Rest² |
|
> 15 bis 35 |
|
|||
I |
1 |
|
|
100 |
|
|
|
MIG, WIG, Plasmaschweißen, Wurzelschutz |
inert |
2 |
|
|
|
100 |
|
|
|||
3 |
|
|
Rest² |
> 0 bis 95 |
|
|
|||
M1 |
1 |
> 0 bis 5 |
|
Rest² |
|
> 0 bis 5 |
|
MAG |
schwach oxidierend |
2 |
> 0 bis 5 |
|
Rest² |
|
|
|
|||
3 |
|
> 0 bis 3 |
Rest² |
|
|
|
|||
4 |
> 0 bis 25 |
> 0 bis 3 |
Rest² |
|
|
|
|||
M2 |
1 |
> 0 bis 25 |
|
Rest² |
|
|
|
|
|
2 |
|
> 3 bis 10 |
Rest² |
|
|
|
|||
3 |
> 0 bis 5 |
> 3 bis 11 |
Rest² |
|
|
|
|||
4 |
> 0 bis 25 |
> 0 bis 8 |
Rest² |
|
|
|
|||
M3 |
1 |
> 25 bis 50 |
|
Rest² |
|
|
|
|
|
2 |
|
> 10 bis 15 |
Rest² |
|
|
|
|||
3 |
>5 bis 50 |
> 8 bis 15 |
Rest² |
|
|
|
|||
C |
1 |
100 |
|
|
|
|
|
stark oxidierend |
|
2 |
Rest |
> 0 bis 30 |
|
|
|
|
|||
F |
1 |
|
|
|
|
|
100 |
Plasmaschneiden, Wurzelschutz |
reaktionsträge |
2 |
|
|
|
|
> 0 bis 50 |
Rest |
reduzierend |
Einteilung der Schutzgase für Lichtbogenschweißen und -schneiden
Werkstoffe zum WIG-Schweißen
- Besonderheiten verschiedener Werkstoffe
- Un- und niedriglegierte Stähle
- Austenitsche CrNi-Stähle
- Aluminium und Aluminiumlegierungen
- Kupfer und Kupferlegierungen
- Sonstige Werkstoffe
Besonderheiten verschiedener Werkstoffe
Es wurde schon gesagt, dass das WIG-Verfahren sich für das Schweißen einer großen Palette von Werkstoffen eignet. Einige Werkstoffe werden dabei mit Gleichstrom, andere mit Wechselstrom geschweißt. Im Folgenden werden einige Besonderheiten behandelt, die sich bei den verschiedenen Werkstoffen ergeben.
Un- und niedriglegierte Stähle
Diese Stähle lassen sich mit allen Schmelzschweißverfahren fügen. Bei der Auswahl des Schweißverfahrens sind aber meist weniger Qualitätsgesichtspunkte als vielmehr wirtschaftliche Überlegungen entscheidend. Das WIG-Verfahren ist deshalb wegen seiner geringen Leistung bei diesen Stählen unterrepräsentiert. Eine Ausnahme macht das Schweißen von Wurzellagen. Bei Wanddicken größer etwa 6mm wird oft nur die Wurzel WIG-geschweißt und die übrigen Lagen werden mit einem leistungsfähigeren Verfahren eingebracht. Eine andere Ausnahme ist das Schweißen von Rohrleitungen mit kleineren Durchmessern. Hierfür gibt es nichts, was sich besser dafür eignen würde als das WIG-Verfahren. Eine Besonderheit ist, dass es zur Porenbildung kommen kann, z.B. bei unlegierten Rohrstählen (z.B. P235), die wenig Silizium enthalten oder beim Einschweißen solcher Rohre in Kesselböden. Auch bei Tiefziehstählen, die nur mit Aluminium beruhigt sind, können Poren auftreten, wenn mit wenig Zusatzwerkstoff geschweißt wird. Durch Sauerstoffaufnahme aus der Atmosphäre, die auch beim Schutzgasschweißen nicht völlig zu verhindern ist, wird das Schweißgut unberuhigt und es können Poren durch KohIenmonoxidbildung im Schweißgut auftreten. Die Abhilfe besteht darin, möglichst viel Si / Mn-legierten Zusatzwerkstoff einzubringen, wodurch der Sauerstoff unschädlich abgebunden wird.
Austenitische CrNi-Stähle
Diese Werkstoffe eignen sich besonders gut zum WIG-Schweißen, weil durch die günstige Viskosität des Schweißgutes feingefiederte, glatte Oberraupen und flache Wurzelunterseiten entstehen. Durch die relativ langsame Schweißgeschwindigkeit des WIG-Verfahrens und die geringe Wärmeleitfähigkeit der CrNi- Stähle kann es bei kleinen Wanddicken aber leicht zu Überhitzungen kommen. Dadurch können Heißrisse auftreten, auch die Korrosionsbeständigkeit kann vermindert werden. Überhitzungen können wenn notwendig durch Einlegen von Abkühlungspausen oder Kühlen der Werkstücke vermieden werden. Dadurch verringert sich auch der Verzug, der gerade bei CrNi-Stählen wegen des höheren Ausdehnungskoeffizienten größer ist als bei unlegiertem Stahl. Bei Bauteilen, die später einem Korrosionsangriff ausgesetzt sind, müssen die nach dem Schweißen auf der Oberfläche der Naht und auf den Rändern beiderseits im Grundwerkstoff zurückbleibenden Oxidhäute und Anlauffarben durch Bürsten, Strahlen, Schleifen oder Beizen entfernt werden, bevor das Bauteil in Betrieb geht. Unter diesen Häuten kommt es sonst zu einem verstärkten Korrosionsangriff. Dies gilt auch für die Wurzelseite beim Schweißen von Rohren. Da eine mechanische Bearbeitung hier schlecht möglich ist, empfiehlt sich die Vermeidung der Oxidation durch Formieren.
Aluminium und Aluminiumlegierungen
Beim Schweißen von Aluminiumwerkstoffen wird, von Ausnahmen abgesehen auf die später noch eingegangen wird, Wechselstrom zum Schweißen verwendet. Dies ist erforderlich, um die hochschmelzende Oxidschicht auf dem Bauteil zu beseitigen. Aluminiumoxid (AI2O3) hat einen Schmelzpunkt von etwa 2050°C. Der Grundwerkstoff z.B. Reinaluminium schmilzt dagegen schon bei 650°C. Aluminium hat eine so große chemische Verwandtschaft zu Sauerstoff, sodass sich, selbst wenn die Oberfläche des Grundwerkstoffs vor dem Schweißen durch Bürsten oder Schaben oxidfrei gemacht wurde, auf der Badoberfläche schnell wieder solche Häute bilden. Diese schmelzen wegen ihres hohen Schmelzpunktes nur direkt unter dem Lichtbogen teilweise auf. Der größte Teil der Nahtoberfläche wäre beim Schweißen mit Gleichstrom (-Pol) also mit einer festen Schicht von Aluminiumoxid bedeckt. Diese macht die Badbeobachtung unmöglich und erschwert die Zugabe von Zusatzwerkstoff. Zwar könnte diese Oxidschicht durch Verwenden von Flussmitteln, wie beim Löten beseitigt werden, dies würde aber einen zusätzlichen Aufwand bedeuten.
Beim Schweißen mit Wechselstrom bietet sich die Möglichkeit, diese Oxidschicht durch Ladungsträger im Lichtbogen aufzureißen und zu beseitigen. Dafür kommen nur die lonen infrage, da die Elektronen wegen ihrer geringen Masse nicht genügend kinetische Energie dafür besitzen. Wenn der Minuspol an der Elektrode liegt, wandern die Elektronen von der Elektrode zum Werkstück und die Restionen vom Werkstück zur Elektrode. Bei dieser Polung ist eine Reinigungswirkung nicht möglich. Bei umgekehrter Polung treffen dagegen die schwereren lonen auf die Werkstückoberfläche. Sie können durch ihre kinetische Energie die Oxidschicht aufreißen und beseitigen. Das Schweißen am heißeren Pluspol hätte aber zur Folge, dass die Strombelastbarkeit der Elektrode nur sehr gering wäre. Diese Variante des WIG-Schweißens ist deshalb nur für das Schweißen sehr dünner Aluminiumstrukturen (bis etwa 2,5 mm Wanddicke) brauchbar. Als Kompromiss bietet sich der Wechselstrom an. Wenn die positive Halbwelle an der Elektrode liegt, tritt die Reinigungswirkung ein. In der danach folgenden negativen Halbwelle kann die Elektrode dann wieder abkühlen. Man spricht deshalb auch von der Reinigungs- und der Kühlhalbwelle. Die Strombelastbarkeit ist beim Schweißen an Wechselstrom geringer als beim Gleichstrom- Minuspolschweißen. Sie ist aber wesentlich höher als beim Schweißen am Pluspol. Es hat sich gezeigt, dass für eine ausreichende Reinigungswirkung gar nicht die ganze positive Halbwelle benötigt wird, sondern dass 20 oder 30% davon ausreichen.
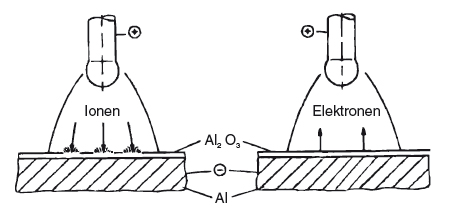
Reinigung durch kinetische Energie | Elektrode am Pluspol |
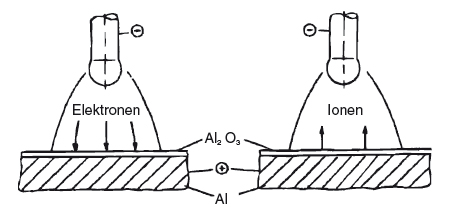
Keine Reinigung | Elektrode am Minuspol |
Dies hat man sich bei modernen WIG-Stromquellen zu Nutze gemacht. Diese erzeugen einen künstlichen rechteckförmigen Wechselstrom, in dem mittels schnell reagierender Schalter (Transistoren) wechselseitig der Plus- und der Minuspol einer Gleichstromquelle auf die Elektrode geschaltet wird. Dabei kann man dann die Balance der beiden Halbwellen zueinander z.B. von 20% Plus / 80% Minus bis 80% Plus / 20% Minus verändern. Der geringere Anteil des Pluspols führt zu einer höheren Strombelastbarkeit der Elektrode bzw. bei gleicher Stromeinstellung zu einer längeren Standzeit. Bei diesen sogenannten ”Square-Wave- Quellen” kann meist auch die Frequenz des künstlichen Wechselstromes noch verändert werden, z.B. zwischen 50 und 300 Hz. Auch mit dem Erhöhen der Frequenz ist eine Schonung der Elektrode verbunden.
Der rechteckförmige künstliche Wechselstrom hat aber noch einen weiteren Vorteil. Da der Stromverlauf beim Wechsel der Polarität sehr steil ist, sind die Totzeiten des Lichtbogens beim Nulldurchgang wesentlich kürzer als bei einem sinusförmigen Verlauf. Das Wiederzünden erfolgt deshalb sicherer, sogar ohne Zündhilfe, und der Lichtbogen ist insgesamt stabiler. Allerdings machen sich die Wiederzündvorgänge als stärkeres Brummgeräusch bemerkbar. Moderne WIG-Stromquellen gestatten das Schweißen mit Gleichstrom, sowie mit sinusförmigem und mit rechteckförmigen Wechselstrom. In neuerer Zeit wird auch eine Variante des WIG-Minuspolschweißens angewendet, bei der hochheliumhaltiges Schutzgas (z.B. 90% He / 10% Ar) verwendet wird. Beim Schweißen am Minuspol läßt sich wie bereits geschildert, die Oxidhaut nicht aufbrechen. Durch die hohe Temperatur des energiereicheren Heliumlichtbogens kann sie aber verflüssigt werden. Damit ist sie nur noch wenig störend. Das WIG-Gleichstrom-Minuspolschweißen unter Helium wird wegen des besseren Einbrandverhaltens vor allem bei Reparaturschweißungen an Gussteilen aus Aluminium-Silizium-Legierungen angewendet.
Eine weitere Besonderheit beim Schweißen des Werkstoffes Aluminium ist seine Porenempfindlichkeit bei der Aufnahme von Wasserstoff. Die Verhältnisse sind wesentlich kritischer als beim Schweißen von Stahl. Während Eisen beim Übergang vom flüssigen in den festen Zustand noch eine Lösungsfähigkeit für Wasserstoff von 8 cm3/100 g Schweißgut besitzt, hat Aluminium im festen Zustand praktisch keine Lösungsfähigkeit für Wasserstoff mehr. Das heißt, der gesamte Wasserstoff, der beim Schweißen aufgenommen wurde, muss das Schweißgut verlassen bevor es erstarrt. Anderenfalls entstehen Poren im Schweißgut.
Quellen für Wasserstoff beim WIG-Schweißen von Aluminium sind in erster Linie Oxidhäute auf dem Grundwerkstoff. Diese binden Feuchtigkeit und müssen deshalb vor dem Schweißen durch Bürsten oder Schaben entfernt werden. Andererseits ist der Lichtbogen ruhiger, wenn sich eine dünne Oxidhaut auf der Oberfläche befindet, weil diese leichter Elektronen aussendet als das reine Metall. Es muss deshalb ein Kompromiss gefunden werden, zwischen einem stabilen Lichtbogen und einer ausreichenden Porensicherheit. Es hat sich als günstig erwiesen, die Werkstückoberflächen vor dem Schweißen gründlich von Oxiden zu befreien, danach aber mit dem Schweißen noch eine oder zwei Stunden zu warten, damit sich eine dünne Oxidschicht neu bilden kann. Auch die auf der Oberfläche der Schweißstäbe gebildeten Oxidhäute tragen zur Porenbildung bei. Zusatzwerkstoffe aus Aluminium sollten deshalb sorgfältig und nicht zu lange gelagert werden.
Kuper und Kupferlegierungen
Das Schweißen von Kupfer wird vor allem durch seine große Wärmeleitfähigkeit erschwert. Deshalb muss bei größeren Werkstoffdicken zumindest am Schweißnahtbeginn vorgewärmt werden. Später ergibt sich ein Vorwärmeffekt durch die voranlaufende Schweißwärme, sodass ein großflächiges Vorwärmen nur bei Wanddicken > 5 mm erforderlich ist. Das WIG Verfahren bietet die Möglichkeit den Lichtbogen selbst zum Vorwärmen zu benutzen, in dem man am Schweißnahtbeginn durch kreisende Bewegungen mit dem verlängerten Lichtbogen Wärme einbringt. Reinkupfer und viele Cu-Legierungen werden mit Gleichstrom, Elektrode am Minuspol geschweißt. Nur einige Bronzen wie Messing und Aluminiumbronze lassen sich besser mit Wechselstrom schweißen.
Sonstige Werkstoffe
Außer den bereits besprochenen Werkstoffen werden noch in nennenswertem Maße Nickel und Nickellegierungen WIG-geschweißt. Die wichtigsten sind Nickel / Chrom-Legierungen (z.B. Inconel) und Nickel / Kupfer-Legierungen (z.B. Monel). Ferner werden Titan und Titanlegierungen WIG-geschweißt. Auch für diese Werkstoffe eignet sich am besten Gleichstrom mit negativ gepolter Elektrode. Beim Schweißen von Titan muss aber nicht nur der Schweißnahtbereich selbst durch Schutzgas geschützt werden, sondern auch in weiterer Entfernung von der Schweißstelle und gegebenenfalls auch auf der Rückseite muss durch Schleppbrausen Schutzgas zugegeben werden, um Anlauffarben zu vermeiden. Der Werkstoff versprödet sonst durch Aufnahme atmosphärischer Gase.
Farbkennzeichnung Wolframelektroden
Kennzeichnung | Gewicht Oxid in % | Oxid | Farbe | Im Lieferprogramm |
WP | - | - | Grün | |
WT 4 | 0,35 - 0,55 | Th | Hellblau | nein |
WT 10 | 0,80 - 1,20 | Th | Gelb | nein |
WT 20 | 1,70 - 2,20 | Th | Rot | nein |
WT 30 | 2,80 - 3,20 | Th | Lila | nein |
WT 40 | 3,80 - 4,20 | Th | Orange | nein |
WZ 3 | 0,15 - 0,50 | Zr | Braun | nein |
WZ 8 | 0,70 - 0,90 | Zr | Weiß | nein |
WL 10 | 0,90 - 1,20 | La | Schwarz | auf Anfrage |
WL 15 | 1,40 - 1,60 | La | Gold | |
WL 20 | 1,80 - 2,20 | La | Dunkelblau | |
WC 20 | 1,80 - 2,20 | Ce | Grau | |
WR 2* | Mischoxide | Seltene Erden | Türkis | |
E3® | Mischoxide | Seltene Erden | Lila |
* WR 2 zur Zeit noch nicht standardisiert
Th: Thorium; Zr: Zirconium; La: Lanthanoxid; Ce: Ceroxid
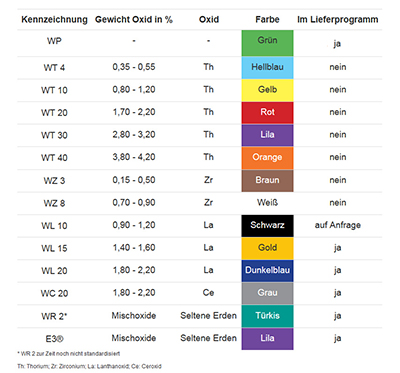
WP-Elektroden:
- Reine Wolframelektroden
- Wechselstromschweißen von Aluminiumlegierungen
- Nicht geeignet zum Gleichstromschweißen
WT-Elektroden:
- Leicht radioaktiv strahlend aufgrund von Thoriumzusatz
- Aufgrund erhöhter Gesundheitsbelastung ist vom Einsatz abzusehen
- Verbesserte Zündeigenschaften und höhere Stromtragfähigkeit gegenüber WP-Elektroden
WZ-Elektroden:
- Dank Zirkoniumzusatz geringere Gefahr von Schmelzverunreinigung
- Wolframelektroden zum Wechselstromschweißen von Aluminiumlegierungen
- Nur bedingt zum Gleichstromschweißen geeignet
WL-Elektroden:
- Erhöhte Zündfähigkeit dank Lanthanoxid
- Geeignet zum Gleich- und Wechselstromschweißen
- Einsetzbar für un- und hochlegierte Stähle, Aluminium-, Titan-, Nickel-, Kupfer- und Magnesiumlegierungen sowie für das Microplasmaschweißen
- Optimal für den Einsatz im Niederstrombereich
- Guter Ersatz für WT-Elektroden
WC-Elektroden:
- Dank Ceroxid sehr gute Zünd- und Wiederzündeigenschaften
- Geeignet zum Gleich- und Wechselstromschweißen
- Einsetzbar für un- und hochlegierte Stähle, Aluminium-, Titan-, Nickel-, Kupfer- und Magnesiumlegierungen im unteren und mittleren Strombereich
- Guter Ersatz für WT-Elektroden
WS-Elektroden:
- Unterschiedliche, nicht genormte Zusammensetzung
- Geeignet zum Gleich- und Wechselstromschweißen
- Einsetzbar für un- und hochlegierte Stähle, Aluminium-, Titan-, Nickel-, Kupfer- und Magnesiumlegierungen im unteren und mittleren Strombereich
- Hohe Standzeit und hohe Belastbarkeit