Grundlagen des MIG-MAG-Schweißens – Theorie und Praxis am MIG-MAG-Schweißgerät
- Allgemeines zum MIG-MAG-Schweißen
- Stromart
- Tipps zum richtigen MIG-MAG-Schweißen
- Zünden des Lichtbogens
- Brennerführung
- Beenden des Schweißens
- Schweißparameter
- Benötigte Ausrüstung
Allgemeines
Der nach ISO 857-1 für Deutschland neue Oberbegriff für alle Lichtbogenschweißverfahren, bei denen eine Drahtelektrode unter Schutzgas abgeschmolzen wird, ist gasgeschütztes Metall-Lichtbogenschweißen (Prozess-Nr.13). In Deutschland war der Oberbegriff früher Metall-Schutzgasschweißen. Die ISO-Norm erklärt das Verfahren aus dem Englischen übersetzt wie folgt: Metall-Lichtbogenschweißen unter Benutzung einer Drahtelektrode, wobei der Lichtbogen und das Schweißbad vor der Atmosphäre geschützt werden durch eine Gasumhüllung aus einer externen Quelle. Nach der Art des verwendeten Schutzgases wird dann weiter unterteilt in Metall-Inertgasschweißen (MIG), Prozess-Nr.131, wenn ein inertes Gas verwendet wird und Metall-Aktivgasschweißen(MAG), Prozess-Nr. 135, wenn ein aktives Gas eingesetzt wird.
Als weitere Varianten werden in ISO 857-1 noch aufgezählt: Fülldrahtschweißen mit aktivem Gas (Prozess-Nr. 136), Fülldrahtschweißen mit inertem Gas (Prozess-Nr. 137), Plasma-MIG-Schweißen (Prozess-Nr. 151) und Elektrogasschweißen (Prozess-Nr. 73). Das MIG-MAG-Schweißen ist dadurch gekennzeichnet, dass eine von der Spule durch einen Vorschubmotor zugeführte Drahtelektrode kurz vor dem Austritt aus dem Brenner durch die Stromdüse mit Strom versorgt wird, so dass der Lichtbogen zwischen Drahtelektrodenende und Werkstück brennen kann. Das Schutzgas strömt aus der Schutzgasdüse aus, welche die Drahtelektrode konzentrisch umgibt.
Dadurch wird das Schweißgut vor dem Zutritt der atmosphärischen Gase Sauerstoff, Wasserstoff und Stickstoff geschützt. Das Schutzgas hat neben der Schutzfunktion auch noch andere Aufgaben. Da es die Zusammensetzung der Lichtbogenatmosphäre bestimmt, beeinflusst es auch deren elektrische Leitfähigkeit und damit die Schweißeigenschaften. Ferner beeinflusst es durch Zu- und Abbrandvorgänge die chemische Zusammensetzung des entstehenden Schweißgutes, hat also auch eine metallurgische Wirkung.
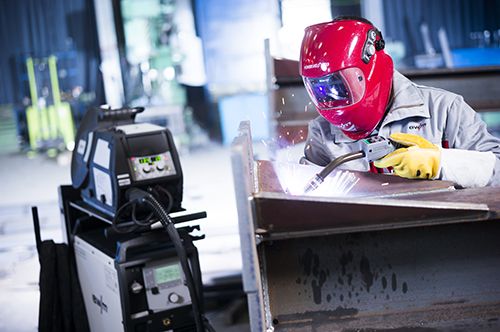
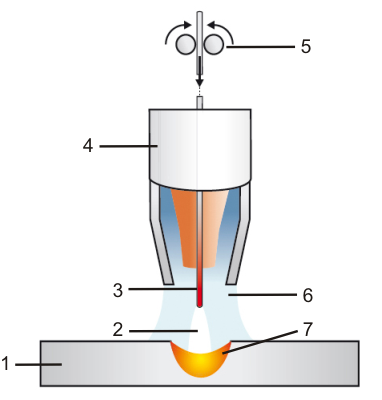
- Werkstück
- Lichtbogen
- Drahtelektrode
- Gasdüse
- Drahtvorschub
- Schutzgas
- Schmelzbad
Stromart
Von neueren Ausnahmen abgesehen, wird das MIG-MAG-Schweißen mit Gleichstrom ausgeführt, wobei der Pluspol der Stromquelle an der Elektrode und der Minuspol am Werkstück liegt. Bei einigen Fülldrähten wird auch schon mal mit umgekehrter Polarität geschweißt. In neuerer Zeit wird für sehr spezielle Anwendungsfälle, z.B. zum MIG Schweißen sehr dünner Aluminiumbleche, auch Wechselstrom eingesetzt.
Tipps zum richtig MIG-MAG-Schweißen
Der MIG- oder MAG-Schweißer benötigt eine gute Ausbildung, nicht nur im praktischen Schweißen, sondern auch hinsichtlich der theoretischen Besonderheiten des Verfahrens. Dies hilft ihm Fehler zu vermeiden.
Zünden des Lichtbogens
Nach Betätigung des Brennerschalters setzt sich die Drahtelektrode mit der vorher eingestellten Geschwindigkeit in Bewegung.
Gleichzeitig wird sie über das Stromrelais stromführend gemacht und das Schutzgas beginnt zu strömen. Beim Berühren der Werkstückoberfläche entsteht ein Kurzschluss. Wegen der hohen Stromdichte an der Elektrodenspitze beginnt an der Berührungsstelle Material zu verdampfen und der Lichtbogen zündet.
Bei hohen Drahtförderraten kann der zunächst noch sehr schwache Lichtbogen durch den nachdrückenden Drahtwerkstoff wieder erstickt werden, so dass das Zünden erst nach dem zweiten oder dritten Anlauf gelingt.
Es ist deshalb zweckmäßiger mit verminderter Fördergeschwindigkeit zu zünden und erst wenn der Lichtbogen stabil brennt, auf die eigentliche Drahtfördergeschwindigkeit hochzuschalten. Neuzeitliche MIG/MAG-Anlagen bieten die Möglichkeit, eine sogenannte "Einschleichgeschwindigkeit" einzustellen.
Das Zünden sollte nie außerhalb der Fuge und nur an solchen Stellen erfolgen, die unmittelbar danach wieder aufgeschmolzen werden. Von nicht überschweißten Zündstellen kann wegen der hohen Abkühlungsgeschwindigkeit solcher örtlich erwärmten Stellen Rissbildung ausgehen.
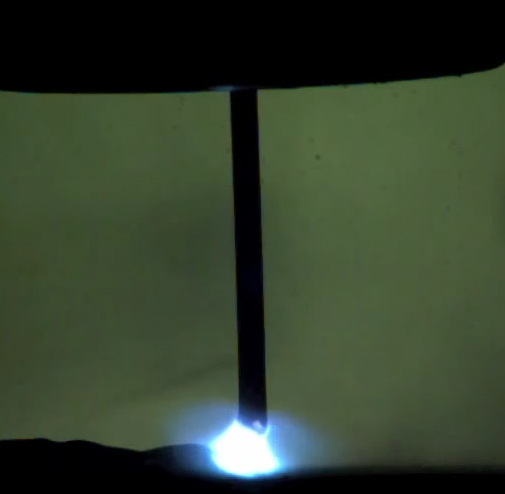
Brennerführung
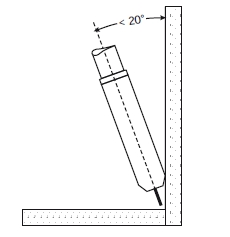
Der Brenner wird in Schweißrichtung etwa 10 ° bis 20 ° geneigt und kann schleppend oder stechend geführt werden. Sein Abstand zum Werkstück soll so sein, dass das freie Drahtende, d.h. der Abstand zwischen der Unterkante der Stromdüse und dem Ansatzpunkt des Lichtbogens, etwa 10 - 12 x Drahtdurchmesser [mm] beträgt. Bei zu stark geneigtem Brenner besteht die Gefahr, dass Luft in das Schutzgas eingesaugt wird.
Stechende Brennerführung ist in der Regel üblich beim Schweißen mit Massivdrähten, schleppende Führung beim Einsatz von schlackenführenden Fülldrähten. Leicht schleppend wird der Brenner generell auch in der Position PG geführt. Fallnahtschweißen (Pos. PG) kommt hauptsächlich bei dünneren Blechen vor.
Bei dickeren Blechen besteht die Gefahr, dass durch vorlaufendes Schweißgut Bindefehler entstehen. Bindefehler durch vorlaufendes Schweißgut können auch in anderen Positionen auftreten, wenn mit zu geringer Schweißgeschwindigkeit geschweißt wird. Breites Pendeln sollte deshalb, von der Position PF abgesehen, möglichst vermieden werden. Die übliche Pendelform ist das offene Dreieck.
Beenden des Schweißens
Am Ende der Naht darf der Lichtbogen nicht plötzlich abgeschaltet und der Brenner vom Endkrater weggezogen werden. Vor allem bei dickeren Blechen, wo in großvolumigen Raupen tiefe Endkrater entstehen können, ist es günstiger den Lichtbogen langsam vom Bad abzuziehen oder, wenn die verwendete Anlage dies hergibt, ein Endkraterfüllprogramm einzustellen. Bei den meisten Anlagen kann auch eine gewisse Nachströmzeit des Schutzgases eingestellt werden, damit das letzte noch flüssige Schweißgut unter der Schutzgasabdeckung erstarren kann. Dies ist aber nur wirksam, wenn der Brenner auch eine Zeit lang am Ende der Naht verweilt.
Schweißparameter
Die untere Grenze der möglichen Anwendung des Verfahrens für Stumpfnähte liegt bei unlegiertem Stahl bei etwa 0,7 mm, bei nichtrostendem Stahl bei 1 mm und bei Aluminiumwerkstoffen bei etwa 2 mm. Wurzellagen und Dünnbleche werden meist mit dem Kurzlichtbogen geschweißt oder im unteren Leistungsbereich des Impulslichtbogens. Für Füll-, Deck- und Gegenlagen an dickeren Blechen wird dann mit höherer Leistung der Sprüh- oder Langlichtbogen eingestellt.
Diese Schweißarbeiten können aber auch sehr spritzerarm mit dem Impulslichtbogen ausgeführt werden. Die dem Schweißer zur Information dienenden Strom- und Spannungswerte können an den, meist in die Geräte eingebauten Messinstrumenten abgelesen werden. Beim Impulsschweißen zeigen die Anzeigeinstrumente den sich aus Impuls- und Grundphase bei der eingestellten Pulsfrequenz ergebenden arithmetischen Mittelwert von Stromstärke und Lichtbogenspannung an.
Die Tabellen können deshalb auch als Richtwerte für das MIG/MAG-Impulsschweißen dienen. Sind keine Messgeräte eingebaut, kann mit externen Messgeräten gemessen werden, oder der Schweißer muss sich nach der ebenfalls in den Tabellen angegebenen Drahtvorschubgeschwindigkeit richten. Die richtige Lichtbogenlänge muss er dann nach dem einstellen, was er sieht und hört.
Zum erfolgreichen MIG-MAG-Schweißen benötigen Sie die nachstehende Ausrüstung:
Weitere Informationen zum Thema MIG-MAG-Schweißen finden Sie in unserem Schweißlexikon.