Grundlagen des WIG-Schweißens – Theorie und Praxis am WIG-Schweißgerät
- Wissenswertes zum WIG-Schweißen
- Auswahl des Schweißzusatzes
- Einstellen der Schutzgasmenge
- Reinigung der Werkstückoberfläche
- Zünden des Lichtbogens
- Führen des WIG-Brenners
- Schweißposition
- Schweißparameter
- Schweißen mit Stromimpulsen
- Benötigte Ausrüstung
Wissenswertes zum WIG-Schweißen
Im Hinblick auf die zu verarbeitenden Werkstoffe, Wanddicken und Schweißpositionen ist das WIG-Schweißen ein universell einsetzbares Schweißverfahren. Es ermöglicht, Schweißverbindungen in höchster Qualität zu erzeugen. Das WIG-Schweißverfahren – die volle Bezeichnung für dieses Verfahren lautet nach DIN 1910 – Teil 4 Wolfram- Inertgasschweißen – stammt aus den USA und wurde dort 1936 unter dem Namen Argonarc-Schweißen bekannt. Erst nach dem 2. Weltkrieg wurde es in Deutschland eingeführt. In den englisch sprechenden Ländern heißt das Verfahren TIG nach englisch ”Tungsten” für Wolfram. Das Verfahren zeichnet sich gegenüber anderen Schmelzschweißverfahren durch eine Reihe von interessanten Vorteilen aus. Es ist z.B. universell anwendbar.
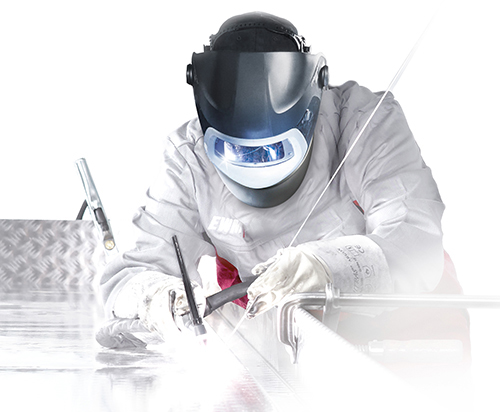
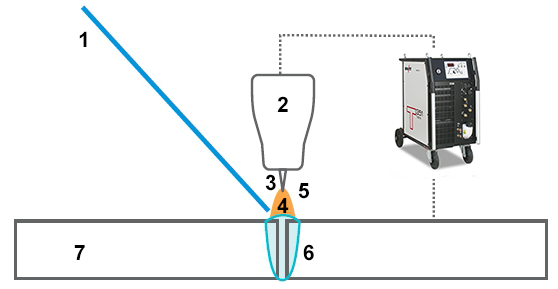
- Schweißstab
- Brenner
- Wolframelektrode
- Lichtbogen
- Schutzgas
- Schmelzbad
- Grundwerkstoff
Wenn ein metallischer Werkstoff überhaupt schmelzschweißgeeignet ist, dann lässt er sich mit diesem Verfahren fügen. Zum anderen ist es ein sehr ”sauberes” Verfahren, das kaum Spritzer und nur wenig Schadstoffe erzeugt und bei richtiger Anwendung eine qualitativ hochwertige Schweißverbindung garantiert. Ein besonderer Vorteil des WIG-Schweißens ist auch, dass hier gegenüber anderen Verfahren, die mit abschmelzender Elektrode arbeiten, die Zugabe von Schweißzusatz und die Stromstärke entkoppelt sind. Der Schweißer kann deshalb seinen Strom optimal auf die Schweißaufgabe abstimmen und nur so viel Schweißzusatz zugeben, wie gerade erforderlich ist. Dies macht das Verfahren besonders geeignet zum Schweißen von Wurzellagen und zum Schweißen in Zwangslagen. Die genannten Vorteile haben dazu geführt, dass das WIG-Verfahren heute in vielen Bereichen der Industrie und des Handwerks mit Erfolg eingesetzt wird. Es erfordert allerdings bei der manuellen Anwendung ein geschicktes ”Händchen” des Schweißers und eine gute Ausbildung. Diese Anleitung will über die Besonderheiten des Verfahrens aufklären und vielleicht auch Interesse wecken bei den Firmen, die es trotz Vorliegens entsprechender Schweißaufgaben noch nicht anwenden.
Auswahl des Schweißzusatzes
Der Schweißzusatz beim WIG-Schweißen liegt meist stabförmig vor, beim vollmechanischen Einsatz des Verfahrens wird er drahtförmig durch ein separates Vorschubwerk zugeführt. In der Regel werden die Schweißzusätze artgleich zum Grundwerkstoff ausgewählt. Manchmal ist es aber aus metallurgischen Gründen erforderlich, daß der Zusatz bei einigen Legierungselementen etwas vom Grundwerkstoff abweicht. Dies ist z.B. beim Kohlenstoffgehalt der Fall, der aus Gründen der Risssicherheit, wenn eben möglich, sehr niedrig gehalten wird. In solchen Fällen spricht man von artähnlichen Schweißzusätzen. Es gibt aber auch Fälle, wo artfremde Zusätze erforderlich sind. Dies ist z.B. der Fall beim Fügen von schwerschweißbaren C-Stählen, wo austenitische Schweißzusätze oder sogar Nickelbasislegierungen verwendet werden. Der Durchmesser des Schweißzusatzes muß auf die Schweißaufgabe abgestimmt sein. Er richtet sich nach der Materialdicke und damit auch nach dem Durchmesser der Wolframelektrode. Die Schweißstäbe sind in der Regel 1000 mm lang. Sie werden in Bünden geliefert und sollten einzeln mit der DIN- oder der Handelsbezeichnung gekennzeichnet sein, um Verwechslungen zu vermeiden.
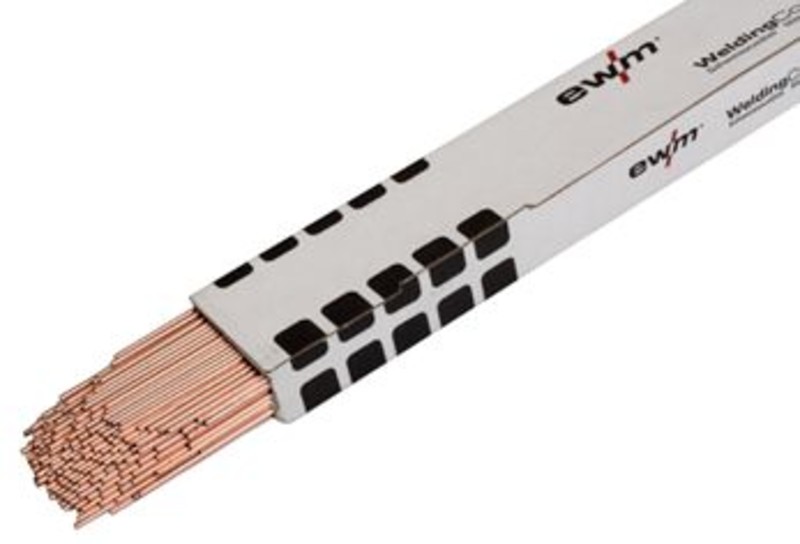
Einstellen der Schutzgasmenge
Die Schutzgasmenge wird als Volumenstrom in I/min eingestellt. Dieser richtet sich nach der Größe des Schmelzbades und damit nach dem Elektrodendurchmesser, dem Gasdüsendurchmesser, dem Düsenabstand zur Grundwerkstoffoberfläche, der umgebenden Luftströmung und der Art des Schutzgases – siehe auch Abschnitt Schutzgase. Eine Faustregel sagt, daß bei Argon als Schutzgas und den am meisten verwendeten Wolframelektrodendurchmessern von 1 bis 4 mm je Minute 5 bis 10 Liter Schutzgas zugegeben werden sollten. Das Messen der Durchflussmenge kann indirekt mit Manometern erfolgen, die den der Durchflußmenge proportionalen Druck vor einer eingebauten Staudüse messen. Die Skala des Manometers ist dann direkt in I/min geeicht. Genauer sind Messgeräte, die mittels Glasröhrchen und Schwebekörper direkt in dem zum Brenner fließenden Schutzgasstrom messen.
Reinigung der Werkstückoberfläche
Für ein gutes Schweißergebnis ist es wichtig, die Fugenflanken und die Oberfläche des Werkstückes im Schweißbereich vor dem Beginn des Schweißens gründlich zu säubern. Die Oberflächen sollten metallisch blank und frei von Fett, Schmutz, Rost und Farbe sein. Auch Zunderschichten sollten nach Möglichkeit entfernt werden. In vielen Fällen wird dazu ein Bürsten ausreichen. Wo dies nicht genügt, muß die Oberfläche durch Schleifen oder ein mechanisches Bearbeitungsverfahren behandelt werden. Bei korrosionsbeständigen Werkstoffen dürfen nur Bürsten aus nichtrostendem Stahl verwendet werden, weil sonst Fremdrost durch Eisenteilchen entstehen kann, die in die Oberfläche eingetragen wurden. Bei Aluminium ist es aus Gründen der Porenentstehung besonders wichtig, daß keine dickeren Oxidhäute auf der Oberfläche verbleiben. Zum Säubern und Entfetten sind geeignete Lösungsmittel zu benutzen. Achtung: Bei Verwendung chlorhaltiger Lösungsmittel können giftige Dämpfe entstehen.
Zünden des Lichtbogens
Der Lichtbogen sollte nie außerhalb der Fuge auf dem Grundwerkstoff gezündet werden, sondern stets so, daß die Zündstelle unmittelbar danach beim Schweißen wieder aufgeschmolzen wird. Zu Beginn des Schweißens kühlt der hocherhitzte Grundwerkstoff an der Zündstelle nämlich durch den Wärmeentzug der rückwärtigen kalten Massen sehr schnell ab. Die Folge dieser raschen Abkühlung können Aufhärtungen, eventuell schon mit Rissen verbunden, und Poren sein. Die schnelle Abkühlung läßt sich vermeiden wenn das Zünden direkt am Beginn der Schweißnaht erfolgt und eventuell entstandene Ungänzen sofort wieder aufgeschmolzen werden. Die Kontaktzündung sollte die absolute Ausnahme sein, wenn das verwendete ältere Schweißgerät nicht über eine Zündhilfe (Hochspannungsimpulszündung) verfügt. In diesem Fall wird auf einem in die Fuge in der Nähe des Schweißnahtbeginns eingelegten Kupferplättchen gezündet. Von dort wird der Lichtbogen dann zum beabsichtigten Nahtanfang gezogen und das Schweißen beginnt. Bei einer Berührungszündung direkt auf dem Grundwerkstoff kann Wolfram ins Schweißgut gelangen, das wegen des hohen Schmelzpunktes nicht aufgeschmolzen wird und später im Durchstrahlungsfilm wegen der größeren Absorption der Röntgenstrahlen durch Wolfram als helle Stelle zu erkennen ist.
Führen des WIG-Brenners
(s. Abb. rechts)
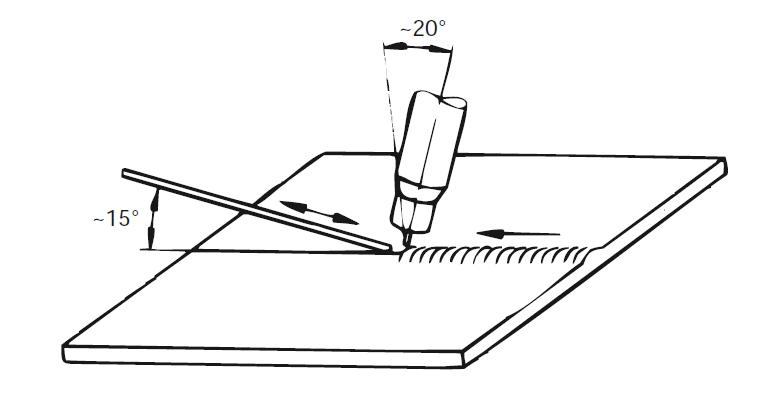
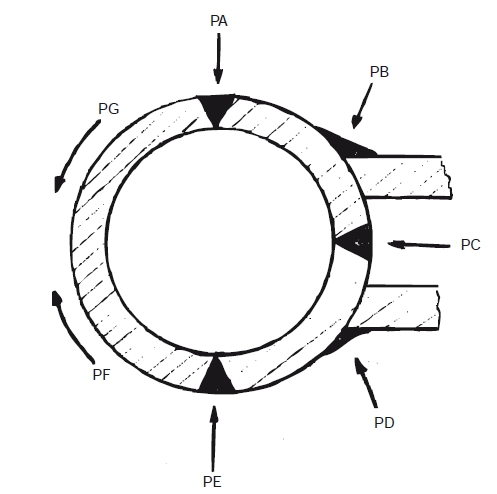
Schweißposition
Nach ISO 6947 werden die Schweißpositionen mit PA – PG bezeichnet. Diese sind, wenn man Sie an einem Rohr betrachtet von oben (PA) ausgehend im Uhrzeigersinne alphabetisch angeordnet Die Position PA ist das, was früher in Deutschland mit waagerecht oder Wannenlage bezeichnet wurde. Es folgen dann die Stumpfnahtpositionen PC (horizontal an senkrechter Wand) und PE (überkopf), sowie die Kehlnahtpositionen PB (horizontal) und PD (horinzontal/ überkopf). Beim Schweißen von Blechen bedeutet PF, das senkrecht steigend geschweißt wird, PG ist die Fallnaht. Am Rohr sind aber darunter mehrere Positionen zusammengefaßt. Die Position PF gilt, wenn das Rohr von der Überkopfposition ausgehend ohne Drehen nach beiden Seiten steigend geschweißt wird., bei der Position PG gilt dies sinngemäß für die Schweißung von oben nach unten (Fallnaht). Das WIG Schweißen ist in allen Positionen möglich. Die Schweißdaten müssen dabei, wie auch bei anderen Schweißverfahren auf die Position abgestimmt werden.
Schweißparameter
Die untere Grenze der Anwendbarkeit des WIG-Verfahrens liegt bei Stahl bei etwa 0,3 mm, bei Aluminium und Kupfer bei 0,5 mm. Nach oben hin sind der Anwendung höchstens wirtschaftliche Grenzen gesetzt. Die Abschmelzleistung des Verfahrens ist nicht sehr groß. Deshalb werden oft nur die Wurzellagen WIG geschweißt und die übrigen Lagen mit anderen Verfahren (E, MAG), die eine höhere Leistung haben, eingebracht. Bei der Wahl der Schweißparameter muß man sich vergegenwärtigen, daß am Schweißgerät nur die Stromstärke eingestellt wird, die Lichtbogenspannung ergibt sich aus der Lichtbogenlänge, die der Schweißer einhält. Dabei gilt, daß die Spannung mit zunehmender Lichtbogenlänge größer wird. Als Anhaltswert für eine zum Durchschweißen ausreichende Stromstärke gilt beim Schweißen von Stahl mit Gleichstrom (-Pol) eine Stromstärke von 45 Ampere pro mm Wanddicke. Beim Wechselstromschweißen von Aluminium werden 40 Ampere/mm benötigt.
Schweißen mit Stromimpulsen
Beim Schweißen mit impulsförmigem Strom wechseln Stromstärke und Spannung im Rhythmus der Impulsfrequenz ständig zwischen einem niedrigen Grundwert und dem höheren Impulswert. Unter Einwirkung des hohen Impulsstromes wird der Einbrand in den Grundwerkstoff erzeugt und es bildet sich ein punktförmiges Schmelzbad aus. Dieses beginnt unter Einwirkung des folgenden niedrigeren Grundstromes bereits vom Rand ausgehend zu erstarren, bis der nächste Stromimpuls es wieder aufschmilzt und vergrößert. Inzwischen ist der Lichtbogen aber bereits in Schweißgeschwindigkeit weiter gewandert, so dass die Schweißnaht beim WIG Impulsschweißen aus vielen sich überlappenden Schweißpunkten gebildet wird. Die Größe des Schmelzbades ist dabei im Durchschnitt kleiner als beim Schweißen mit gleichförmigem Strom, so dass es sich in Zwangslagen besser beherrschen lässt. Trotzdem ist ausreichender Einbrand gewährleistet. Der eben geschilderte Effekt tritt aber nur auf, wenn ein ausreichender Temperaturunterschied im Schmelzbad zwischen Grund- und Impulsphase auftritt. Dies ist nur bei Impulsfrequenzen unter etwa 5 Hz gegeben. Als Nachteil kann genannt werden, dass die Schweißgeschwindigkeit vielfach beim Impulsschweißen verringert werden muss. Auch nimmt der Schweißer das Pulsen im niedrigen Frequenzbereich als störendes Flackern des Lichtbogens wahr. Deshalb wird diese Variante des WIG-Schweißens weniger beim manuellen Schweißen angewandt, wo der Schweißer andere Möglichkeiten hat die Badbeherrschung zu beeinflussen, als vielmehr beim mechanisierten WIG Schweißen.
Zum erfolgreichen WIG Schweißen benötigen Sie die nachstehende Ausrüstung:
WIG Schweißgerät
Brenner
Werkstückklemme / Massezange
Stabelelektrode
Schweißwerkzeuge
Arbeitsschutzkleidung
Der Inhalt soll umfangreiche Informationen über das WIG-Schweißen vermitteln und beschreibt verschiedene Aspekte des Verfahrens, geht jedoch nicht auf spezifische Funktionen wie Puls und AC/DC ein. Die technischen Details und Anleitungen zielen eher darauf ab, das Verständnis und die Praxis des Schweißverfahrens zu fördern. Konkrete Erwähnungen oder Empfehlungen für spezifische Schweißgeräte sind nicht vorhanden.
Die umfassenden Erklärungen sind sowohl für Anfänger als auch für erfahrene Schweißer geeignet, da sie die Grundlagen bis hin zu fortgeschrittenen Techniken und Parametereinstellungen abdecken. Dabei werden professionelle Tipps und detaillierte Anleitungen gegeben, die auch für Hobby-Schweißer wertvoll sind. Der Text bedient die Interessen einer Zielgruppe, die Wert auf Präzision und technisches Verständnis legt.
Weitere Informationen zum Thema WIG-Schweißen finden Sie in unserem Schweißlexikon.
Zusatzwerk-, Hilfs- und Werkzeugstoffe
- Drahtelektrodensorten
- Un- und niedriglegierte Stähle
- Hochlegierte Stähle und Nickelbasislegierungen
- Aluminium und Aluminiumlegierung
- Sonstige Werkstoffe
Drahtelektrodensorten
Drahtelektroden für das MIG/MAG-Schweißen von unlegierten Stählen und Feinkornbaustählen sind in DIN EN 440 genormt. Die Norm unterscheidet nach der chemischen Zusammensetzung 11 Sorten von Schweißdrähten. Sie enthält aber auch solche Schweißdrahtsorten, die nur in anderen Ländern Europas üblich sind. In Deutschland werden für unlegierte Stähle nur die Sorten G2Si1, G3Si1 und G4Si1 in nennenswertem Umfang verwendet. Diese enthalten in der genannten Reihenfolge zunehmende Gehalte an Silizium und Mangan, und zwar im Mittel von 0,65 bis 0,9 % Silizium und von 1,10 bis 1,75 % Mangan. Für Feinkornstähle kommen auch die Sorten G4Mo und G3Ni1 und G3Ni2 zur Anwendung. Fülldrahtelektroden zum Schweißen dieser Stähle enthält DIN EN 758. Nach der Zusammensetzung der Füllung unterscheidet man hier Rutiltypen, basische Typen und Metallpulver-Typen. Neben den Fülldrähten zum MIG/MAG-Schweißen sind in DIN EN 758 aber auch selbstschützende Fülldrähte genormt, die ohne zusätzlich zugegebenes Schutzgas verschweißt werden. Sie werden häufig zum Auftragschweißen verwendet. Drahtelektroden für das Schweißen warmfester Stähle sind in DIN EN 12070,Fülldrahtelektroden für diese Stähle in DIN EN 12071 genormt. Die Drahtelektroden reichen von der nur molybdänlegierten Variante über die Drähte mit 1,2,5, 5 und 9 % Chrom bis zur Drahtelektrode mit 12 % Chrom. An weiteren Legierungselementen sind Molybdän, Vanadin und Wolfram vorhanden. Fülldrahtelektroden gibt es bis zu 5 % Chrom. Drahtelektroden zum Schweißen nichtrostender und hitzebeständiger Stähle sind in DIN EN 12072 genormt; Fülldrahtelektroden für diese Stähle in DIN EN 12073. Die Normen unterscheiden Zusätze für martensitische / ferritische Chromstähle, austenitische Stähle, ferritische/ austenitische Stähle und vollaustenitische hochkorrosionsbeständige Stähle, ferner spezielle Typen und hitzebeständige Typen.
Werkstoffe zum MIG/MAG-Schweißen
Un- und niedriglegierte Stähle
Un- und niedriglegierte Stähle werden unter Mischgasen M1, M2, M3 oder unter reinem Kohlendioxid geschweißt. Wegen der geringeren Spritzerbildung, vor allem im oberen Leistungsbereich, dominieren in Deutschland aber die Mischgase. Diese Stähle lassen sich im allgemeinen gut mit dem MAG-Verfahren schweißen. Eine Ausnahme bilden hochkohlenstoffhaltige Sorten, wie E 360, mit ca. 0,45 % C. Durch den großen Einbrand des Prozesses nimmt das Schweißgut durch Vermischung relativ viel Kohlenstoff auf und es kommt dadurch zu einer Gefährdung durch Heißrisse. Abhilfe ist möglich durch alle Maßnahmen, welche den Einbrand und damit die Vermischung reduzieren. Dazu zählen niedrige Stromstärken ebenso wie Schweißen auf dem etwas vorlaufenden Schweißgut - Vorsicht: Bindefehlergefahr. Porenbildung entsteht bei un- und niedriglegierten Stählen hauptsächlich durch Stickstoff. Dieser kann durch Aufmischung beim Schweißen von Stählen mit hohem Stickstoffgehalt stammen, z.B. bei nitrierten Stählen. Meist wird der Stickstoff aber infolge einer unvollständigen Schutzgasglocke aus der Luft aufgenommen. Ein sicherer Schutz ist gewährleistet, wenn die richtige Schutzgasmenge eingestellt wurde und Verwirbelungen des Schutzgasstromes, z.B. durch Spritzer in der Schutzgasdüse oder Instabilitäten des Prozesses, vermieden werden. Kohlendioxid als Schutzgas ist weniger empfindlich gegen diese Art der Porenbildung als Mischgase. Bei Mischgasen nimmt die Empfindlichkeit mit steigendem CO2-Gehalt ab.
Hochlegierte Stähle und Nickelbasislegierungen
Auch diese Werkstoffgruppe lässt sich prinzipiell mit dem MIG/MAG-Prozess gut schweißen. Als Schutzgase kommen für hochlegierte Stähle Argon / Sauerstoff-Gemische mit 1-5 % Sauerstoff (M1.1) oder Argon mit CO2-Gehalten bis zu 2,5% (M1.2) zur Anwendung. Einen bedeutenden Nachteil stellen beim Schweißen korrosionsbeständiger Stähle die Oxidhäute dar, die nach dem Schweißen auf und neben der Naht zurückbleiben. Diese müssen vollständig durch Bürsten, Beizen oder Strahlen entfernt werden bevor das Bauteil in Betrieb geht, weil sie die Korrosionsbeständigkeit verschlechtern. Der Säuberungsaufwand ist bei MAG-geschweißten Nähten größer als beim E-Hand-Schweißen, wo die Schlackenabdeckung dem Sauerstoff bei höheren Temperaturen noch den Zutritt zur Nahtoberfläche verwehrt. Ein Teil der wirtschaftlichen Vorteile des teilmechanischen Schweißens kann deshalb durch die höheren Nacharbeitungskosten wieder verloren gehen. CO2-haltige Mischgase verhalten sich in dieser Hinsicht etwas günstiger als O2-haltige. Sie werden deshalb zunehmend angewendet. Der Kohlendioxidanteil im Schutzgas darf aber nicht zu hoch werden, weil das im Lichtbogen zerfallende Gas zur Aufkohlung des Schweißgutes führt und damit zu einer Herabsetzung der Korrosionsbeständigkeit. Der zulässige CO2-Gehalt ist deshalb auf max. 5 % begrenzt. Beim Schweißen korrosionsbeständiger Stähle muss jede Überhitzung vermieden werden, weil sie durch Ausscheidung von Chromkarbid zur Versprödung und zur Herabsetzung der Korrosionsbeständigkeit führen kann. Es muss deshalb das Wärmeeinbringen kontrolliert und dem Werkstoff eventuell durch Einlegen von Abkühlungspausen Gelegenheit zum Zwischenabkühlen geboten werden. Bei den Werkstoffen aus der Gruppe der vollaustenitischen Stähle ist "kaltes" Schweißen auch zur Vermeidung von Heißrissen angesagt. Da austenitische Stähle durch Wasserstoff nicht verspröden, können dem Argon zur Leistungssteigerung (Erhöhung der Schweißgeschwindigkeit) auch einige Prozent Wasserstoff beigemischt werden. Wegen der Porengefahr sollte der H2-Gehalt aber nicht über 7 % liegen. Duplexstähle , die eine Zweiphasen-Struktur aus Austenit und Ferrit besitzen, neigen dagegen wieder mehr zu wasserstoffinduzierter Rissbildung. Nickelbasislegierungen werden in der Regel unter Argon MIG-geschweißt. Bei Reinnickel und einigen Legierungen können geringe Wasserstoffzusätze die Oberflächenspannungen verringern und so die Nahtzeichnung verbessern.
Aluminium und Aluminiumlegierungen
Aluminiumwerkstoffe werden grundsätzlich MIG-geschweißt. Als Schutzgas kommt im Regelfall Argon zur Anwendung. Wegen der großen Wärmeleitfähigkeit des Aluminiums wirken sich hier Heliumzugaben besonders günstig aus. Helium verbessert, wie bereits erwähnt, die Wärmeleitfähigkeit und den Wärmeinhalt der Schutzgasatmosphäre. Dies bringt einen tieferen und breiteren Einbrand. Wo der tiefere Einbrand nicht gebraucht wird, z. B. beim Schweißen dünner Bleche, kann bei gleicher Einbrandform entsprechend schneller geschweißt werden. Dickere Querschnitte von Aluminium müssen wegen der großen Wärmeleitfähigkeit des Werkstoffes vorgewärmt werden. Dies sichert nicht nur ausreichenden Einbrand, sondern verringert auch die Porenanfälligkeit, weil das Schweißgut mehr Zeit zum Entgasen während des Erstarrens hat. Bei Verwendung von heliumhaltigen Schutzgasen - üblich sind Gehalte von 25 oder 50 % - kann die Vorwärmung verringert werden, bzw. bei geringeren Wanddicken kann ganz auf das Vorwärmen verzichtet werden. Dies gleicht den höheren Preis der heliumhaltigen Gase teilweise wieder aus. Schwierigkeiten, die hochschmelzende Oxidhaut auf dem Bad zu beseitigen, bestehen beim MIG-Schweißen nicht, weil der Pluspol an der Elektrode liegt (katodische Reinigung). Trotzdem ist es ratsam, die Oxidhäute unmittelbar vor dem Schweißen durch Schaben oder Bürsten zu entfernen, da sie hygroskopisch sind und daher Wasserstoff ins Schweißgut bringen. Wasserstoff ist die alleinige Ursache für Porenbildung beim Schweißen von Aluminiumwerkstoffen. Aluminium hat im flüssigen Zustand eine relativ große Löslichkeit für Wasserstoff, im festen Zustand ist dieses Gas dagegen fast gar nicht im Metall löslich. Jeglicher Wasserstoff, der beim Schweißen aufgenommen wurde, muss deshalb das Schweißgut vor der Erstarrung verlassen, wenn keine Poren auftreten sollen. Dies ist vor allem bei dickeren Querschnitten nicht immer möglich. Gänzlich porenfreie Nähte sind deshalb, wenn größere Wanddicken vorliegen, bei Aluminiumwerkstoffen nicht zu erreichen. Die günstige Wirkung einer Vorwärmung wurde schon vorher erwähnt. AlMg- und AlSi-Legierungen neigen bei Si-Gehalten von etwa 1 % bzw. Mg-Gehalten von etwa 2 % zur Heißrissigkeit beim Schweißen. Dieser Legierungsbereich sollte durch Auswahl des Schweißzusatzes vermieden werden. Meist verhält sich die nächst höher legierte Drahtelektrode besser als eine artgleiche.
Sonstige Werkstoffe
Außer den schon genannten Werkstoffen werden noch Kupfer und Kupferlegierungen in nennenswertem Maße MIG-geschweißt. Reinkupfer muss wegen der großen Wärmeleitfähigkeit relativ hoch vorgewärmt werden, um Bindefehler zu vermeiden. Das Schweißgut von Bronzedrähten, z.B. solche aus Aluminium- oder Zinnbronze, besitzt gute Gleiteigenschaften. Es wird deshalb für Auftragsschweißungen an Gleitflächen verwendet. Bei solchen Schweißungen auf Eisenwerkstoffen muss der Einbrand durch geeignete Maßnahmen gering gehalten werden, weil Eisen in Kupfer nur eine geringe Löslichkeit hat. Es wird in Form von Kügelchen im Schweißgut eingeschlossen und vermindert die Gebrauchseigenschaften. Ähnlich sind die Bedingungen beim MIG-Löten. Dieses Verfahren wird z.B. zum Verbinden verzinkter Bleche im Automobilbau eingesetzt. Als Zusätze werden Drahtelektroden aus Silizium- oder Zinnbronze verwendet. Durch den niedrigeren Schmelzpunkt dieser Bronzen wird die Zinkverdampfung verringert. Es entstehen weniger Poren und der Schutz durch die Zinkschicht bleibt bis nahe an die Naht heran und auch auf der Rückseite der Bleche erhalten. Auch hierbei sollte möglichst kein Einbrand in den Stahlwerkstoff hinein entstehen, sondern die Bindung sollte, wie beim Hartlöten, nur durch Diffusions- und Adhäsionskräfte erfolgen. Dies wird durch angepasste Schweißparameter und eine besondere Brennerhaltung erreicht, wodurch der Lichtbogen nur auf dem flüssigen Schmelzbad brennt.
Grundlagen des MIG-MAG-Schweißens – Theorie und Praxis am MIG-MAG-Schweißgerät
- Allgemeines zum MIG-MAG-Schweißen
- Stromart
- Tipps zum richtigen MIG-MAG-Schweißen
- Zünden des Lichtbogens
- Brennerführung
- Beenden des Schweißens
- Schweißparameter
- Benötigte Ausrüstung
Allgemeines
Der nach ISO 857-1 für Deutschland neue Oberbegriff für alle Lichtbogenschweißverfahren, bei denen eine Drahtelektrode unter Schutzgas abgeschmolzen wird, ist gasgeschütztes Metall-Lichtbogenschweißen (Prozess-Nr.13). In Deutschland war der Oberbegriff früher Metall-Schutzgasschweißen. Die ISO-Norm erklärt das Verfahren aus dem Englischen übersetzt wie folgt: Metall-Lichtbogenschweißen unter Benutzung einer Drahtelektrode, wobei der Lichtbogen und das Schweißbad vor der Atmosphäre geschützt werden durch eine Gasumhüllung aus einer externen Quelle. Nach der Art des verwendeten Schutzgases wird dann weiter unterteilt in Metall-Inertgasschweißen (MIG), Prozess-Nr.131, wenn ein inertes Gas verwendet wird und Metall-Aktivgasschweißen(MAG), Prozess-Nr. 135, wenn ein aktives Gas eingesetzt wird.
Als weitere Varianten werden in ISO 857-1 noch aufgezählt: Fülldrahtschweißen mit aktivem Gas (Prozess-Nr. 136), Fülldrahtschweißen mit inertem Gas (Prozess-Nr. 137), Plasma-MIG-Schweißen (Prozess-Nr. 151) und Elektrogasschweißen (Prozess-Nr. 73). Das MIG-MAG-Schweißen ist dadurch gekennzeichnet, dass eine von der Spule durch einen Vorschubmotor zugeführte Drahtelektrode kurz vor dem Austritt aus dem Brenner durch die Stromdüse mit Strom versorgt wird, so dass der Lichtbogen zwischen Drahtelektrodenende und Werkstück brennen kann. Das Schutzgas strömt aus der Schutzgasdüse aus, welche die Drahtelektrode konzentrisch umgibt.
Dadurch wird das Schweißgut vor dem Zutritt der atmosphärischen Gase Sauerstoff, Wasserstoff und Stickstoff geschützt. Das Schutzgas hat neben der Schutzfunktion auch noch andere Aufgaben. Da es die Zusammensetzung der Lichtbogenatmosphäre bestimmt, beeinflusst es auch deren elektrische Leitfähigkeit und damit die Schweißeigenschaften. Ferner beeinflusst es durch Zu- und Abbrandvorgänge die chemische Zusammensetzung des entstehenden Schweißgutes, hat also auch eine metallurgische Wirkung.
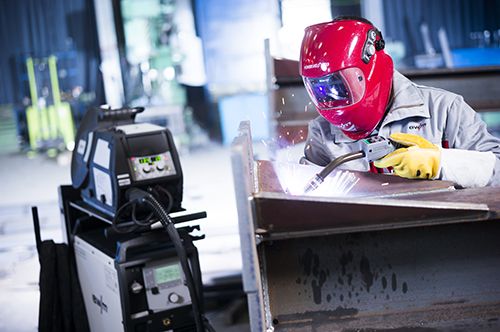
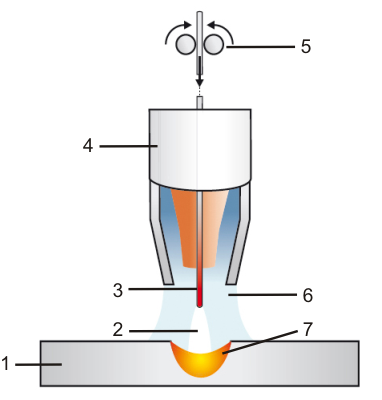
- Werkstück
- Lichtbogen
- Drahtelektrode
- Gasdüse
- Drahtvorschub
- Schutzgas
- Schmelzbad
Stromart
Von neueren Ausnahmen abgesehen, wird das MIG-MAG-Schweißen mit Gleichstrom ausgeführt, wobei der Pluspol der Stromquelle an der Elektrode und der Minuspol am Werkstück liegt. Bei einigen Fülldrähten wird auch schon mal mit umgekehrter Polarität geschweißt. In neuerer Zeit wird für sehr spezielle Anwendungsfälle, z.B. zum MIG Schweißen sehr dünner Aluminiumbleche, auch Wechselstrom eingesetzt.
Tipps zum richtig MIG-MAG-Schweißen
Der MIG- oder MAG-Schweißer benötigt eine gute Ausbildung, nicht nur im praktischen Schweißen, sondern auch hinsichtlich der theoretischen Besonderheiten des Verfahrens. Dies hilft ihm Fehler zu vermeiden.
Zünden des Lichtbogens
Nach Betätigung des Brennerschalters setzt sich die Drahtelektrode mit der vorher eingestellten Geschwindigkeit in Bewegung.
Gleichzeitig wird sie über das Stromrelais stromführend gemacht und das Schutzgas beginnt zu strömen. Beim Berühren der Werkstückoberfläche entsteht ein Kurzschluss. Wegen der hohen Stromdichte an der Elektrodenspitze beginnt an der Berührungsstelle Material zu verdampfen und der Lichtbogen zündet.
Bei hohen Drahtförderraten kann der zunächst noch sehr schwache Lichtbogen durch den nachdrückenden Drahtwerkstoff wieder erstickt werden, so dass das Zünden erst nach dem zweiten oder dritten Anlauf gelingt.
Es ist deshalb zweckmäßiger mit verminderter Fördergeschwindigkeit zu zünden und erst wenn der Lichtbogen stabil brennt, auf die eigentliche Drahtfördergeschwindigkeit hochzuschalten. Neuzeitliche MIG/MAG-Anlagen bieten die Möglichkeit, eine sogenannte "Einschleichgeschwindigkeit" einzustellen.
Das Zünden sollte nie außerhalb der Fuge und nur an solchen Stellen erfolgen, die unmittelbar danach wieder aufgeschmolzen werden. Von nicht überschweißten Zündstellen kann wegen der hohen Abkühlungsgeschwindigkeit solcher örtlich erwärmten Stellen Rissbildung ausgehen.
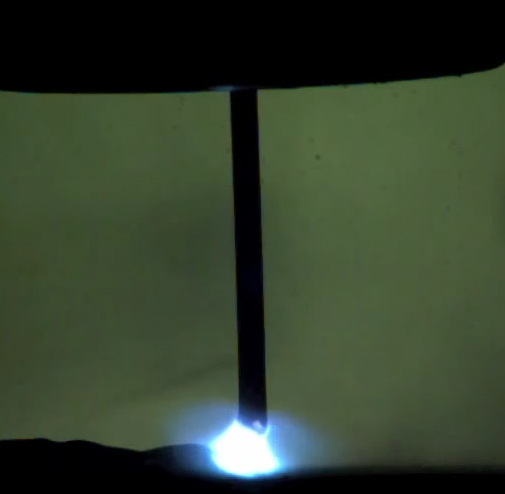
Brennerführung
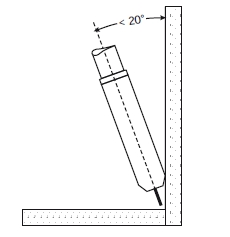
Der Brenner wird in Schweißrichtung etwa 10 ° bis 20 ° geneigt und kann schleppend oder stechend geführt werden. Sein Abstand zum Werkstück soll so sein, dass das freie Drahtende, d.h. der Abstand zwischen der Unterkante der Stromdüse und dem Ansatzpunkt des Lichtbogens, etwa 10 - 12 x Drahtdurchmesser [mm] beträgt. Bei zu stark geneigtem Brenner besteht die Gefahr, dass Luft in das Schutzgas eingesaugt wird.
Stechende Brennerführung ist in der Regel üblich beim Schweißen mit Massivdrähten, schleppende Führung beim Einsatz von schlackenführenden Fülldrähten. Leicht schleppend wird der Brenner generell auch in der Position PG geführt. Fallnahtschweißen (Pos. PG) kommt hauptsächlich bei dünneren Blechen vor.
Bei dickeren Blechen besteht die Gefahr, dass durch vorlaufendes Schweißgut Bindefehler entstehen. Bindefehler durch vorlaufendes Schweißgut können auch in anderen Positionen auftreten, wenn mit zu geringer Schweißgeschwindigkeit geschweißt wird. Breites Pendeln sollte deshalb, von der Position PF abgesehen, möglichst vermieden werden. Die übliche Pendelform ist das offene Dreieck.
Beenden des Schweißens
Am Ende der Naht darf der Lichtbogen nicht plötzlich abgeschaltet und der Brenner vom Endkrater weggezogen werden. Vor allem bei dickeren Blechen, wo in großvolumigen Raupen tiefe Endkrater entstehen können, ist es günstiger den Lichtbogen langsam vom Bad abzuziehen oder, wenn die verwendete Anlage dies hergibt, ein Endkraterfüllprogramm einzustellen. Bei den meisten Anlagen kann auch eine gewisse Nachströmzeit des Schutzgases eingestellt werden, damit das letzte noch flüssige Schweißgut unter der Schutzgasabdeckung erstarren kann. Dies ist aber nur wirksam, wenn der Brenner auch eine Zeit lang am Ende der Naht verweilt.
Schweißparameter
Die untere Grenze der möglichen Anwendung des Verfahrens für Stumpfnähte liegt bei unlegiertem Stahl bei etwa 0,7 mm, bei nichtrostendem Stahl bei 1 mm und bei Aluminiumwerkstoffen bei etwa 2 mm. Wurzellagen und Dünnbleche werden meist mit dem Kurzlichtbogen geschweißt oder im unteren Leistungsbereich des Impulslichtbogens. Für Füll-, Deck- und Gegenlagen an dickeren Blechen wird dann mit höherer Leistung der Sprüh- oder Langlichtbogen eingestellt.
Diese Schweißarbeiten können aber auch sehr spritzerarm mit dem Impulslichtbogen ausgeführt werden. Die dem Schweißer zur Information dienenden Strom- und Spannungswerte können an den, meist in die Geräte eingebauten Messinstrumenten abgelesen werden. Beim Impulsschweißen zeigen die Anzeigeinstrumente den sich aus Impuls- und Grundphase bei der eingestellten Pulsfrequenz ergebenden arithmetischen Mittelwert von Stromstärke und Lichtbogenspannung an.
Die Tabellen können deshalb auch als Richtwerte für das MIG/MAG-Impulsschweißen dienen. Sind keine Messgeräte eingebaut, kann mit externen Messgeräten gemessen werden, oder der Schweißer muss sich nach der ebenfalls in den Tabellen angegebenen Drahtvorschubgeschwindigkeit richten. Die richtige Lichtbogenlänge muss er dann nach dem einstellen, was er sieht und hört.
Zum erfolgreichen MIG-MAG-Schweißen benötigen Sie die nachstehende Ausrüstung:
Weitere Informationen zum Thema MIG-MAG-Schweißen finden Sie in unserem Schweißlexikon.
Welche Elektrode für welchen Zweck?
Bei der Auswahl von Stabelektroden müssen werkstoffliche und schweißtechnische Gesichtspunkte beachtet werden.
Kurzübersicht
Typ
Bezeichnung
Definition
R, RR
Rutil
Standardelektrode mit universellem Einsatz, feintropfiger bis mittlerer Tropfenübergang, gute mechanische Gütewerte, Schweißposition PA, PB, PC, PE, PF, (PG nur begrenzt)
RB
Basisch-rutil
Verwendung als Kombination aus erreichbaren hohen Zähigkeitswerten und einem universellen Einsatz mit erhöhten Anforderungen an den Schweißer und die Nachbearbeitung der Naht
B
Basisch
Verwendung für die Anforderung hoher mechanischer Gütewerte, mittel bis grobtropfiger Tropfenübergang, schlecht lösende Schlacke, möglich in allen Positionen, bitte beachten Sie die Rücktrockenzeit der Elektroden
RC
Rutil-cellulose
Als Ersatz für rein rutile Elektroden verwendet, um auch Schweißposition PG sicher zu beherrschen, geringere Schlackebildung, höhere Anforderungen an den Schweißer und die Nahtnachbearbeitung
C
Cellulose
Überwiegend verwendet für die Wurzellage an Rohrverbindungen (Pipelineschweißung) in Position PG, gute mechanische Gütewerte, mitteltropfig, nahezu keine Schlacke
Auswahl nach schweißtechnischen Gesichtspunkten
Jeder Elektrodentyp hat ganz spezifische Schweißeigenschaften und wird deshalb auch für ganz bestimmte Schweißaufgaben eingesetzt.
Die Zelluloseelektrode (C)
Die Zelluloseelektrode (C) verwendet man wegen ihrer guten Eignung zum Fallnahtschweißen (Pos. PG) zum Schweißen der Rundnähte an Rohren größerer Durchmesser. Bevorzugtes Anwendungsgebiet ist hierbei das Verlegen von Pipelines. Im Vergleich mit dem Schweißen in senkrecht steigender Position (PF) kann man hier schon für die Wurzellage relativ dicke Elektroden (4 mm) einsetzen. Dies bringt wirtschaftliche Vorteile. Der besondere Vorteil des rutilsauren Mischtyps (RA) ist der Schlackenabgang in engen Fugen, wo eine kompakte Schlacke eingeklemmt wird und sich schlecht ablöst. Die Schlacke des RATyps ist in sich porös und zerfällt unter dem Schlackehammer in kleine Stückchen, die sich dann leicht entfernen lassen.
Rutilelektrode (R, RR)
Die besonderen Eigenschaften der Rutilelektrode (R, RR), nämlich das gute Wiederzünden, die leichte Schlackenentfernbarkeit und das gute Nahtaussehen bestimmen ihre Einsatzschwerpunkte. Dies sind Heftarbeiten, sowie das Schweißen von Kehlnähten und Decklagen, wo es auf eine vollständige Schlackenentfernung und auf ein gutes Nahtaussehen ankommt.
Der Rutil-Zellulose-Typ (RC)
Der Rutil-Zellulose-Typ (RC) lässt sich in allen Positionen einschließlich Fallnaht verschweißen. Er ist deshalb universell einsetzbar, besonders unter Montagebedingungen. Vor allem die dickumhüllte Variante, die auch hinsichtlich des Nahtaussehens höhere Anforderungen erfüllt, ist deshalb in kleineren Betrieben oft die All-round-Elektrode.
Die rutilbasische Elektrode (RB)
Die rutilbasische Elektrode (RB) eignet sich wegen ihrer etwas dünneren Umhüllung und deren besonderer Charakteristik besonders gut für das Schweißen von Wurzellagen und das Schweißen in Pos. PF. Ein bevorzugtes Anwendungsgebiet ist deshalb das Verlegen von Rohrleitungen mit kleinen und mittleren Durchmessern.
Die basische Elektrode (B)
Die basische Elektrode (B) eignet sich für das Schweißen in allen Positionen. Spezialtypen sind sogar für das Fallnahtschweißen geeignet. Allerdings fällt das Nahtaussehen etwas gegenüber anderen Typen ab. Dafür hat das Schweißgut aber „innere Werte“. Von allen Elektrodentypen besitzen basische Elektroden die besten Zähigkeitseigenschaften und die beste Risssicherheit des Schweißgutes. Sie werden deshalb dort eingesetzt, wo schwierige Verhältnisse hinsichtlich der Schweißeignung der Grundwerkstoffe vorliegen, z.B. bei Stählen mit eingeschränkter Schweißeignung oder bei großen Wanddicken. Ferner wenn eine große Zähigkeit in der Verbindung gefragt ist, z.B. bei Bauwerken, die im späteren Betrieb tiefen Temperaturen ausgesetzt sind. Der niedrige Wasserstoffgehalt macht diesen Typ auch besonders geeignet zum Schweißen hochfester Stähle.
Auswahl nach werkstofflichen Gesichtspunkten
Die Festigkeits- und Zähigkeitseigenschaften des Grundwerkstoffs müssen in der Regel auch im Schweißgut erreicht werden. Um die Elektrodenauswahl in dieser Hinsicht zu erleichtern sind in der vollständigen Bezeichnung einer Stabelektrode nach DIN EN ISO 2560-A auch Hinweise über die Mindestwerte von Streckgrenze, Zugfestigkeit und Zähigkeit des Schweißgutes und zu einigen Schweißeigenschaften enthalten.
Betrachtet man beispielhaft die Kurzbezeichnung E 46 3 B 42 H5, so hat diese folgende Bedeutung: Die Stabelektrode zum E-Hand- Schweißen (E) hat eine Streckgrenze von mind. 460 N/mm2, eine Zugfestigkeit zwischen 530-680 N/mm2 und eine Mindestdehnung von 20% (46). Eine Kerbschlagarbeit von 47 Joule wird bis zu einer Temperatur von -30°C erreicht (3). Die Elektrode ist basisch umhüllt (B). Nun folgen nicht obligatorisch einige Angaben zum Ausbringen und zur Stromeignung der Elektrode. Die im Beispiel genannte Stabelektrode hat ein Ausbringen von 105 bis 125% und ist nur an Gleichstrom (4) in allen Positionen außer Fallnaht zu verschweißen (2). Der Wasserstoffgehalt des Schweißgutes liegt unter 5 ml / 100 g / Schweißgut (H5). Wenn das Schweißgut außer Mangan noch andere Legierungselemente enthält, dann werden diese vor dem Kurzzeichen für den Umhüllungstyp mit den Kurzzeichen für die chemischen Elemente und evtl. mit Zahlen für den Prozentgehalt angegeben (z.B. 1Ni).
Ein niedriger Wasserstoffgehalt ist wichtig beim Schweißen von Stählen, die zu wasserstoffinduzierter Rissbildung neigen, wie beispielsweise hochfeste Stähle. Hier gibt das Kennzeichen für den Wasserstoffgehalt die notwendigen Informationen.
Ähnliche Bezeichnungssysteme gibt es auch für hochfeste Elektroden (DIN EN ISO 18275), warmfeste Elektroden (DIN EN ISO 3580-A) sowie für nichtrostende Elektroden (DIN EN ISO 3581-A). Bei den warmfesten und nichtrostenden Elektroden müssen neben den Festigkeitseigenschaften aber auch die Warmfestigkeits- bzw. Korrosionseigenschaften der Schweißgüter mit denen der Grundwerkstoffe übereinstimmen. Hierbei gilt deshalb die Regel, dass das Schweißgut möglichst artgleich oder etwas höherlegiert als der Grundwerkstoff sein sollte.
Download Handbuch Schweißzusatzwerkstoffe
Videos
E-Hand (MMA) Grundlagen
- Allgemeines zum E-Hand-Schweißen
- Stromart
- Elektrodentyp
- Eigenschaften der Umhüllungstypen
- Richtig E-Hand Schweißen
- Zünden des Lichtbogens
- Führen der Elektrode
- Magnetische Blaswirkung
- Schweißparameter
- Stromstärken in Abhängigkeit vom Elektrodendurchmesser
- Benötigete Ausrüstung
Allgemeines
Das E-Hand-Schweißen (Prozessnummer 111) zählt zu den Schmelzschweißverfahren und noch näher zugeordnet zu den Metall-Lichtbogenschweißverfahren. ISO 857-1 (Ausgabe 1998) erklärt die Schweißprozesse dieser Gruppe aus dem Englischen übersetzt wie folgt:
Metall-Lichtbogenschweißen: Lichtbogenschweißprozess unter Benutzung einer verbrauchenden Elektrode. Metall-Lichtbogenschweißen ohne Gasschutz: Metall-Lichtbogenschweißprozess ohne extern zugegebenes Schutzgas und Manuelles Metall-Lichtbogenschweißen: Von Hand ausgeführtes Metall- Lichtbogenschweißen unter Benutzung einer umhüllten Elektrode.
In Deutschland nennen wir das zuletzt genannte Verfahren Lichtbogenhandschweißen oder kurz E-Hand-Schweißen (umgangssprachlich auch Elektrodeschweißen). Im englischen Sprachraum ist es unter der Abkürzung MMA oder MMAW (Manual Metal Arc Welding) bekannt. Es ist dadurch gekennzeichnet, dass der Lichtbogen zwischen einer abschmelzenden Elektrode und dem Schmelzbad brennt. Es gibt keinen externen Schutz, jegliche Schutzwirkung vor der Atmosphäre geht von der Elektrode aus. Die Elektrode ist dabei Lichtbogenträger und Schweißzusatz. Die Umhüllung bildet Schlacke und/oder Schutzgas welche u.a. den übergehenden Tropfen und das Schmelzbad vor dem Zutritt der atmosphärischen Gase Sauerstoff, Stickstoff und Wasserstoff schützen.
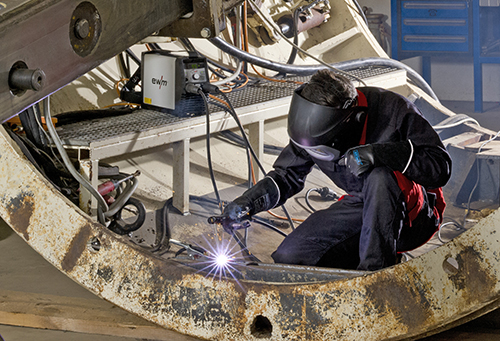
Stromart
Zum Lichtbogenhandschweißen (E-Hand-Schweißen) kann im Prinzip sowohl Gleichstrom, als auch Wechselstrom eingesetzt werden, jedoch lassen sich nicht alle Umhüllungstypen der Stabelektroden an sinusförmigem Wechselstrom verschweißen, z.B. nicht die reinbasischen Elektroden. Beim Schweißen an Gleichstrom wird bei den meisten Elektrodentypen der Minuspol an die Elektrode und der Pluspol ans Werkstück angeschlossen. Eine Ausnahme machen auch hier die basischen Elektroden. Sie lassen sich besser am Pluspol verschweißen. Das Gleiche gilt für bestimmte Fabrikate von Zelluloseelektroden. Näheres dazu kann im Abschnitt Elektrodentypen nachgelesen werden. Die Elektrode ist das Werkzeug des Schweißers. Er führt den an ihr brennenden Lichtbogen in der Schweißfuge und schmilzt dabei die Fugenkanten auf Bild 2. Je nach Fugenart und Grundwerkstoffdicke sind dafür unterschiedliche Stromstärken erforderlich. Da die Strombelastbarkeit der Elektroden, abhängig von ihrem Durchmesser und ihrer Länge begrenzt ist, sind die Stabelektroden in verschiedenen Durchmessern und Längen lieferbar. Tabelle 1 zeigt die in DIN EN 759 genormten Abmessungen. Mit zunehmendem Kernstabdurchmesser können höhere Schweißströme angewendet werden.
Elektrodentypen
Es gibt Stabelektroden mit sehr unterschiedlich zusammengesetzten Umhüllungen. Der Aufbau der Umhüllung bestimmt den Abschmelzcharakter der Elektrode, ihre Schweißeigenschaften und die Gütewerte des Schweißgutes (genauere Informationen im Abschnitt "Welche Elektrode für welchen Zweck" . Nach DIN EN 499 gibt es bei Stabelektroden zum Schweißen von unlegierten Stählen unterschiedliche aufgeführten Umhüllungstypen. Dabei muss unterschieden werden zwischen Grundtypen und Mischtypen. Die verwendeten Buchstaben für die Bezeichnung stammen von den englischen Begriffen her. Hier bedeutet C=cellulose (Zellulose), A=acid (sauer), R=rutile (Rutil) und B=basic (basisch). In Deutschland spielt der Rutiltyp eine dominierende Rolle. Stabelektroden können dünnumhüllt sein, mitteldickumhüllt oder dickumhüllt. Bei den Rutilelektroden, die in allen drei Umhüllungsdicken üblich sind, werden deshalb die dickumhüllten Elektroden zur besseren Unterscheidung mit RR bezeichnet. Bei legierten und hochlegierten Stabelektroden kommt diese Vielfalt von Umhüllungstypen nicht vor. Bei den Stabelektroden zum Schweißen nichtrostender Stähle, die in DIN EN 1600 genormt sind, unterscheidet man z.B. nur zwischen Rutilelektroden und basischen Typen, ebenso bei Stabelektroden zum Schweißen warmfester Stähle (DIN EN 1599), jedoch gibt es auch hier bei den Rutilelektroden rutil-basische Mischtypen, ohne dass dies besonders ausgewiesen wird. Dies ist z. B. der Fall bei Elektroden, die bessere Schweißeigenschaften in Zwangslagen haben. Stabelektroden zum Schweißen hochfester Stähle (DIN EN 757) gibt es nur mit basischer Umhüllung.
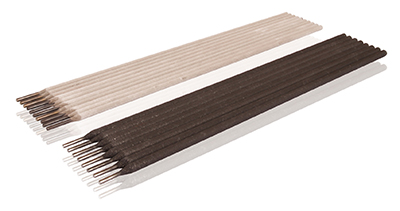
Eigenschaften der Umhüllungstypen
Die Zusammensetzung und die Dicke der Umhüllung beeinflusst in besonderem Maße die Schweißeigenschaften. Dies bezieht sich sowohl auf die Stabilität des Lichtbogens, als auch auf den Werkstoffübergang beim Schweißen und die Viskosität von Schlacke und Schmelzbad. Besonders die Größe der im Lichtbogen übergehenden Tropfen ist dabei von Bedeutung.
Das Bild zeigt schematisch den Tropfenübergang der vier Grundtypen von Umhüllungen: Zellulose (a), Rutil (b), Sauer (c), Basisch (d).
Die Umhüllung besteht überwiegend aus organischen Bestandteilen, die im Lichtbogen verbrennen und dabei Schutzgas zum Schutz der Schweißstelle bilden. Da die Umhüllung außer Zellulose und anderen organischen Stoffen nur geringe Mengen von lichtbogenstabilisierenden Stoffen enthält, entsteht kaum Schlacke. Zellulosetypen sind besonders gut für Fallnahtschweißungen geeignet, weil kein Schlackenvorlauf zu befürchten ist.
Der saure Typ (A), dessen Umhüllung zum größten Teil aus Eisen- und Manganerzen besteht, bietet der Lichtbogenatmosphäre größere Mengen Sauerstoff an. Dieser wird auch vom Schweißgut aufgenommen und verringert dadurch dessen Oberflächenspannung. Die Folge sind ein sehr feiner, sprühregenartiger Werkstoffübergang und ein dünnflüssiges Schweißgut. Elektroden diesen Typs sind deshalb nicht für das Schweißen in Zwangslagen geeignet. Der Lichtbogen ist auch sehr „heißgehend“, gestattet zwar hohe Schweißgeschwindigkeiten, neigt aber zur Bildung von Einbrandkerben. Die beschriebenen Nachteile haben dazu geführt, dass Stabelektroden des reinen sauren Typs in Deutschland kaum noch angewendet werden.
An ihre Stelle ist der rutilsaure Typ (RA) getreten, ein Mischtyp zwischen der sauren und der Rutilelektrode. Die Elektrode hat auch dementsprechende Schweißeigenschaften Die Umhüllung des Rutiltyps (R/RR) besteht zum größten Teil aus Titandioxid in Form der Mineralien Rutil (TiO2) oder Ilmenit (TiO2 . FeO) oder auch von künstlichem Titandioxid. Die Elektroden dieses Typs zeichnen sich aus durch einen fein bis mitteltropfigen Werkstoffübergang, ein ruhiges, spritzerarmes Abschmelzen, eine sehr feine Nahtzeichnung, eine gute Schlackenentfernbarkeit und ein gutes Wiederzündverhalten. Letzteres ist in dieser Form nur bei Rutilelektroden mit hohem Anteil von TiO2 in der Umhüllung zu beobachten. Es bedeutet, dass bei einer bereits einmal angeschmolzenen Elektrode ein Wiederzünden ohne Entfernen des Hüllenkraters möglich ist. Der im Krater gebildete Schlackenfilm hat bei ausreichend hohem TiO2-Gehalt fast eine Leitfähigkeit wie ein Halbleiter, so dass beim Aufsetzen des Kraterrandes auf das Werkstück soviel Strom fließt, dass der Lichtbogen zünden kann, ohne das der Kernstab das Werkstück berührt. Ein solches spontanes Wiederzünden ist immer dann wichtig, wenn der Schweißvorgang, z.B. bei kurzen Nähten, häufig unterbrochen wird.
Neben dem reinen Rutiltyp gibt es bei dieser Gruppe von Elektroden noch einige Mischtypen. Da ist der Rutil-Zellulose- Typ (RC) zu nennen, bei dem ein Teil des Rutils durch Zellulose ersetzt wurde. Da Zellulose beim Schweißen verbrennt, bildet sich weniger Schlacke. Dieser Typ kann deshalb auch in Fallnaht (Pos. PG) verschweißt werden. Er besitzt aber auch gute Schweißeigenschaften in den meisten anderen Positionen.
Ein weiterer Mischtyp ist der rutilbasiche Typ (RB). Er ist etwas dünner umhüllt, als der RR-Typ. Dies und die besondere Schlackencharakteristik macht ihn besonders geeignet zum Schweißen in senkrecht- steigender Position (PF). Bliebe noch der basische Typ (B). Hierbei besteht die Umhüllung zum größten Teil aus den basischen Oxiden des Calziums (CaO) und des Magnesiums (MgO), denen als Schlackenverdünner Flußspat (CaF2) zugegeben wird. Der Flussspat verschlechtert in höheren Gehalten die Wechselstromschweißbarkeit. Reinbasische Elektroden sind deshalb an sinusförmigem Wechselstrom nicht zu verschweißen, jedoch gibt es auch Mischtypen mit weniger Flussspat in der Umhüllung, die an dieser Stromart verwendbar sind. Der Werkstoffübergang der basischen Elektroden ist mittel- bis grobtropfig und das Schmelzbad zähfließend. Die Elektrode ist in allen Positionen gut verschweißbar. Die entstehenden Raupen sind aber wegen der größeren Viskosität des Schweißgutes etwas überwölbt und grober gefiedert. Das Schweißgut hat sehr gute Zähigkeitseigenschaften.
Basische Umhüllungen sind hygroskopisch. Auf besonders sorgfältige, trockene Lagerung der Elektroden ist deshalb zu achten. Feucht gewordene Elektroden müssen rückgetrocknet werden. Das Schweißgut besitzt aber, wenn die Elektroden trocken verschweißt werden, einen sehr niedrigen Wasserstoffgehalt. Neben Stabelektroden mit normalem Ausbringen (<105%) gibt es auch solche, die durch Eisenpulver, das über die Umhüllung zugegeben wird, ein höheres Ausbringen haben, meist >160%. Solche Elektroden werden Eisenpulvertypen oder auch Hochleistungselektroden genannt. Durch ihre große Abschmelzleistung sind sie für viele Anwendungen wirtschaftlicher einzusetzen als Normalelektroden, jedoch ist ihre Anwendung in der Regel auf die waagerechte (PA) und die horizontale Position (PB) beschränkt.
Richtig E-Hand-Schweißen
Der Schweißer benötigt eine gute Ausbildung, und zwar nicht nur in handwerklicher Hinsicht, sondern er muss auch über entsprechendes fachkundiges Wissen verfügen, um Fehler zu vermeiden. Die Ausbildungsrichtlinien des DVS – Deutscher Verband für Schweißen und verwandte Verfahren e.V. sind weltweit anerkannt und wurden inzwischen auch vom Internationalen Schweißverband (IIW) übernommen. Vor dem Beginn des Schweißens werden die Werkstücke in der Regel geheftet. Die Heftstellen müssen so lang und dick ausgeführt werden, dass die Werkstücke sich beim Schweißen nicht unzulässig stark zusammenziehen können und die Heftstellen nicht reißen.

- Werkstück
- Schweißnaht
- Schlacke
- Lichtbogen
- Umhüllte Elektrode
- Elektrodenhalter
- Schweißstromquelle
Zünden des Lichtbogens
Der Schweißprozess wird beim E-Hand- Schweißen durch eine Kontaktzündung eingeleitet. Um den Stromkreis zu schließen muss zunächst zwischen Elektrode und Werkstück ein Kurzschluss erzeugt und die Elektrode sofort danach leicht angehoben werden – der Lichtbogen zündet. Der Zündvorgang sollte nie außerhalb der Fuge erfolgen, sondern grundsätzlich an solchen Stellen, die nach dem Brennen des Lichtbogens sofort wieder aufgeschmolzen werden. An Zündstellen, an denen dies nicht geschieht, können nämlich bei entsprechend empfindlichen Werkstoffen durch die plötzliche Erwärmung Risse entstehen. Bei basischen Elektroden, die zu Ansatzporosität neigen, muss das Zünden sogar deutlich vor dem eigentlichen Schweißanfang erfolgen. Danach wird der Lichtbogen zum Anfangspunkt der Naht zurückgeführt und im weiteren Verlauf des Schweißens werden die ersten abgesetzten Tropfen, die meist porös sind, wieder aufgeschmolzen.
Führen der Elektrode
Die Elektrode wird zur Blechoberfläche senkrecht oder leicht schräg angestellt. Sie wird leicht in Schweißrichtung geneigt. Die sichtbare Lichtbogenlänge, d.h. der Abstand zwischen Kraterrand und Werkstückoberfläche soll dabei etwa dem Kernstabdurchmesser entsprechen. Basische Elektroden müssen mit sehr kurzem Lichtbogen verschweißt werden (Abstand=0,5 x Kernstabdurchmesser). Um dies zu gewährleisten, müssen sie steiler geführt werden als Rutilelektroden. In den meisten Positionen werden Strichraupen geschweißt oder es wird mit nach oben hin größer werdender Fugenbreite leicht gependelt. Nur in der Position PF werden Pendelraupen in der ganzen Breite der Fuge gezogen. In der Regel wird schleppend geschweißt, nur in der Position PF wird die Elektrode stechend angestellt.
- Schweißfuge
- Stabelektrode
- Flüssiges Schweißgut
- Flüssige Schlacke
- Erstarrte Schlacke

Magnetische Blaswirkung
Unter Blaswirkung versteht man eine Erscheinung, bei welcher der Lichtbogen durch Ablenkung aus seiner Mittelachse verlängert wird und dabei ein zischendes Geräusch von sich gibt. Durch diese Ablenkung können Ungänzen entstehen. So kann der Einbrand unzulänglich werden und bei schlackenführenden Schweißprozessen können durch Schlackenvorlauf in der Naht Schlackeneinschlüsse entstehen. Die Ablenkung erfolgt durch Kräfte, die aus dem umgebenden Magnetfeld herrühren. Wie jeder stromdurchflossene Leiter sind auch Elektrode und Lichtbogen von einem ringförmigen Magnetfeld umgeben – dieses wird im Bereich des Lichtbogens beim Übergang in den Grundwerkstoff umgelenkt. Dadurch werden die magnetischen Kraftlinien an der Innenseite verdichtet und an der Außenseite erweitert. Der Lichtbogen weicht in das Gebiet verminderter Flussliniendichte aus. Dabei verlängert er sich und gibt wegen der nun erhöhten Lichtbogenspannung ein zischendes Geräusch von sich. Der Gegenpol übt also eine abstoßende Wirkung auf den Lichtbogen aus. Eine andere magnetische Kraft rührt daher, dass das Magnetfeld sich in einem ferromagnetischen Werkstoff besser ausbreiten kann, als in Luft. Der Lichtbogen wird deshalb von großen Eisenmassen angezogen. Dies zeigt sich z.B. auch dadurch, dass er beim Schweißen auf einem magnetisierbaren Werkstoff an den Blechenden nach Innen abgelenkt wird. Der Ablenkung des Lichtbogens kann man durch entsprechende Schrägstellung der Elektrode begegnen. Da die Blaswirkung beim Schweißen mit Gleichstrom besonders groß ist, kann man sie, wo dies möglich ist, durch das Schweißen an Wechselstrom vermeiden oder zumindest erheblich vermindern. Besonders stark kann die Blaswirkung wegen der umgebenden Eisenmassen beim Schweißen von Wurzellagen werden. Hier hilft es, wenn man den Magnetfluss durch eng beieinander liegende, nicht zu kurze Heftstellen, unterstützt.
Schweißparameter
Beim E-Hand-Schweißen wird nur die Stromstärke eingestellt, die Lichtbogenspannung ergibt sich aus der Lichtbogenlänge, die der Schweißer einhält. Bei der Einstellung der Stromstärke muss die Strombelastbarkeit des verwendeten Elektrodendurchmessers berücksichtigt werden. Dabei gilt die Regel, dass die unteren Grenzwerte für das Schweißen von Wurzellagen und für die Position PF gelten, die oberen dagegen für die übrigen Positionen und für Füll- und Decklagen. Mit zunehmender Stromstärke steigt die Abschmelzleistung und die damit in Zusammenhang stehende Schweißgeschwindigkeit. Auch der Einbrand nimmt mit steigendem Strom zu. Die angegebenen Stromstärken gelten nur für un- und niedriglegierte Stähle. Bei hochlegierten Stählen und Nickelbasiswerkstoffen müssen wegen des größeren elektrischen Widerstandes des Kernstabes niedrigere Werte eingestellt werden.
Stromstärken in Abhängigkeit vom Elektrodendurchmesser
Folgende Faustregeln zur Berechnung der einzelnen Stromstärken in A müssen Sie beachten:
20-40 x Ø
- Bei einem Durchmesser von 2,0 mm sollte die Stromstärke zwischen 40-80 A liegen
- Bei einem Durchmesser von 2,5 mm sollte die Stromstärke zwischen 50-100 A liegen
30-50 x Ø
- Bei einem Durchmesser von 3,2 mm sollte die Stromstärke zwischen 90-150 A liegen
- Bei einem Durchmesser von 4,0 mm sollte die Stromstärke zwischen 120-200 A liegen
- Bei einem Durchmesser von 5,0 mm sollte die Stromstärke zwischen 180-270 A liegen
35-60 x Ø
- Bei einem Durchmesser von 6,0 mm sollte die Stromstärke zwischen 220-360 A liegen
Zum erfolgreichen E-Hand-Schweißen benötigen Sie die nachstehende Ausrüstung:
- Schweißstromquelle
- Elektrodenhalter
- Stabelektrode
- Werkstückklemme / Massezange
- Schweißwerkzeuge
- Arbeitsschutzkleidung
Weitere Informationen zum Thema E-Hand-Schweißen finden Sie in unserem Schweißlexikon.
Normung Schweißzusatzwerkstoffe
EN Norm / DIN EN ISO NORM |
Titel der Norm |
DIN EN 12536 | Stäbe zum Gasschweißen von unlegierten und warmfesten Stählen |
DIN EN 14700 | Schweißzusätze zum Hartauftragen |
DIN EN ISO 636 | Stäbe, Drähte und Schweißgut zum Wolfram-Inertgasschweißen von unlegierten Stählen und Feinkornstählen |
DIN EN ISO 1071 | Schweißzusätze - Umhüllte Stabelektroden, Drähte, Stäbe, und Fülldrahtelektroden zum Schmelzschweißen von Gusseisen |
DIN EN ISO 2560 | Umhüllte Stabelektroden zum Lichtbogenhandschweißen von unlegierten Stählen und Feinkornstählen |
DIN EN ISO 3580 | Umhüllte Stabelektroden zum Lichtbogenhandschweißen von warmfesten Stählen |
DIN EN ISO 14172 | Umhüllte Stabelektroden zum Lichtbogenhandschweißen von Nickel und Nickellegierungen |
DIN EN ISO 14341 | Drahtelektroden und Schweißgut zum Metall-Schutzgasschweißen von unlegierten Stählen und Feinkornstählen |
DIN EN ISO 14343 | Drahtelektroden, Bandelektroden, Drähte und Stäbe zum Lichtbogenschweißen von korrosionsbeständigen und hitzebeständigen Stählen |
DIN EN ISO 16834 | Drahtelektroden, Drähte, Stäbe und Schweißgut zum Schutzgasschweißen von hochfesten Stählen |
DIN EN ISO 17632 | Fülldrahtelektroden zum Metall-Lichtbogenschweißen mit und ohne Schutzgas von unlegierten Stählen und Feinkornstählen |
DIN EN ISO 17633 | Fülldrahtelektroden und Füllstäbe zum Metall-Lichtbogenschweißen mit und ohne Gasschutz von nichtrostenden und hitzebeständigen Stählen |
DIN EN ISO 17634 | Fülldrahtelektroden zum Metall-Schutzgasschweißen von warmfesten Stählen |
DIN EN ISO 18273 | Massivdrähte und -stäbe zum Schmelzschweißen von Aluminium und Aluminiumlegierungen |
DIN EN ISO 18274 | Massivdrähte, -bänder und -stäbe zum Schmelzschweißen von Nickel und Nickellegierungen |
DIN EN ISO 18276 | Schweißzusätze - Fülldrahtelektroden zum Metall-Lichtbogenschweißen mit und ohne Schutzgas von hochfesten Stählen |
DIN EN ISO 21952 | Drahtelektroden, Drähte, Stäbe und Schweißgut zum Schutzgasschweißen von warmfesten Stählen |
DIN EN ISO 24373 | Massivdrähte und -stäbe zum Schmelzschweißen von Kupfer und Kupferlegierungen |
DIN EN ISO 544 | Schweißzusätze - Technische Lieferbedingungen für Schweißzusätze und Pulver – Art des Produktes, Maße, Grenzabmaße und Kennzeichnung |
DIN EN ISO 14175 | Schweißzusätze - Gase und Mischgase für das Lichtbogenschweißen und verwandte Prozesse |
DIN EN ISO 14174 | Schweißzusätze – Pulver zum Unterpulverschweißen und Elektroschlackeschweißen – Einteilung |
DIN EN ISO 24598 | Schweißzusätze – Drahtelektroden, Fülldrahtelektroden und Draht-Pulver-Kombinationen für das Unterpulverschweißen von warmfesten Stählen |
DIN EN ISO 3581 | Schweißzusätze - Umhüllte Stabelektroden zum Lichtbogenhandschweißen von nichtrostenden und hitzebeständigen Stählen - Einteilung |
DIN EN ISO 26304 | Schweißzusätze – Massivdrahtelektroden, Fülldrahtelektroden und Draht-Pulver-Kombinationen zum Unterpulverschweißen von hochfesten Stählen – Einteilung |
DIN EN ISO 14171 | Schweißzusätze – Massivdrahtelektroden, Fülldrahtelektroden und Draht-Pulver-Kombinationen zum Unterpulverschweißen von unlegierten Stählen und Feinkornstählen – Einteilung |