Fundamentos de la soldadura MIG/MAG
- Información general sobre la soldadura MIG/MAG
- Tipo de corriente
- Consejos para una correcta soldadura MIG/MAG
- Encendido del arco voltaico
- Guía de la antorcha
- Finalización de la soldadura
- Parámetros de soldadura
- Equipamiento necesario
Información general
Como se define en ISO 857-1, en Alemania, el nuevo término genérico para todos los procesos de soldadura por arco voltaico, donde un hilo de soldadura se funde utilizando gas de protección, es una soldadura por arco metálico protegido con gas (proceso n.° 13). El término genérico que se utilizaba antes en Alemania era la soldadura metálica protegida con gas. La norma ISO define el proceso de la siguiente manera: Soldadura por arco metálico con utilización de hilo de soldadura, con lo que el arco voltaico y el baño de soldadura quedan protegidos frente a la atmósfera gracias a una envoltura de gas de una fuente externa. Existen otras subclasificaciones en función del tipo de gas de protección utilizado: soldadura bajo atmósfera inerte metálico (MIG), proceso n.º 131, cuando se usa un gas inerte y soldadura metálica de gas activo (MAG), proceso n.º 135, cuando se usa un gas activo.
En la norma ISO 857-1 se enumeran otras variantes: soldadura con hilo tubular con gas activo (proceso n.° 136), soldadura con hilo tubular con gas inerte (proceso n.° 137), soldadura MIG de plasma (proceso n.° 151) y soldadura por electrogás (proceso n.° 73). La soldadura MIG/MAG se caracteriza porque un hilo de soldadura que va desde la bobina por un motor de avance es impulsado por el tubo de contacto poco antes de salir de la antorcha, de manera que el arco voltaico puede arder entre el extremo del hilo de soldadura y la pieza de trabajo. El gas de protección sale de la boquilla del gas de protección que rodea el hilo de soldadura de forma concéntrica.
De este modo, el material de soldadura queda protegido contra la penetración de los gases atmosféricos oxígeno, hidrógeno y nitrógeno. Además de proteger, el gas de protección tiene otras funciones. Como determina la composición de la atmósfera del arco voltaico, también afecta a su conductividad eléctrica y, por ende, a las propiedades de soldadura. Además, debido a los procesos de captación y combustión también influye en la composición química del material de soldadura, con lo que tiene un efecto metalúrgico.
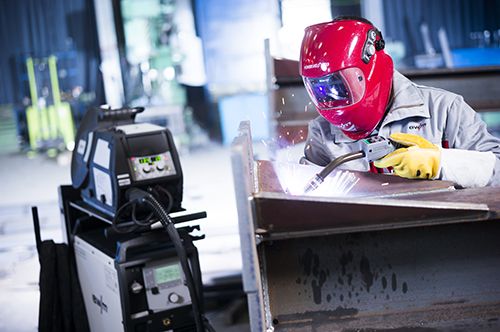
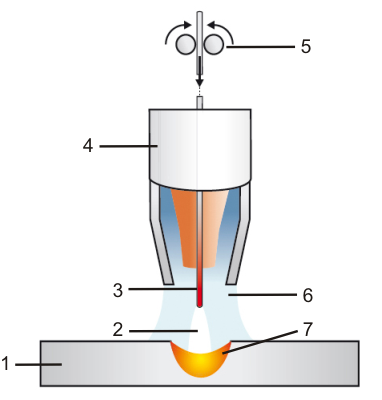
- Pieza de trabajo
- Arco voltaico
- Hilo de soldadura
- Boquilla de gas
- Alimentador de hilo
- Gas de protección
- Baño de soldadura
Tipo de corriente
Salvo algunas excepciones recientes, la soldadura MIG/MAG se realiza con corriente continua, con el polo positivo de la fuente en el electrodo y el polo negativo en la pieza de trabajo. En algunos hilos tubulares también puede soldarse con polaridad inversa. Recientemente, la corriente alterna se utiliza para aplicaciones muy especiales, como soldadura MIG de chapas de aluminio muy finas.
Consejos para una correcta soldadura MIG/MAG
El soldador MIG o MAG precisa de una buena formación, no solo en la soldadura práctica, sino también en cuanto a las características teóricas del procedimiento. Esto le ayudará a evitar errores.
Encendido del arco voltaico
Tras accionar el conmutador de la antorcha, el hilo de soldadura se pone en movimiento con la velocidad previamente establecida.
Al mismo tiempo, contiene voltaje por el relé de corriente y el gas de protección comienza a fluir. Cuando se toca la superficie de la pieza de trabajo, se produce un cortocircuito. Debido a la alta densidad de corriente en la punta del electrodo, el material comienza a vaporizarse en el punto de contacto y el arco voltaico se enciende.
A altas velocidades de alimentación de hilo, el arco todavía muy débil puede ser sofocado por el material del hilo que lo presiona, con lo que el encendido no se producirá hasta el segundo o tercer intento.
Por lo tanto, es más práctico encender a una velocidad de alimentación reducida y no cambiar a la velocidad real de alimentación del hilo hasta que el arco voltaico arda estable. Los últimos sistemas MIG/MAG ofrecen la posibilidad de configurar lo que se conoce como «velocidad de inserción lenta».
La ignición nunca debe realizarse fuera del arco-aire y solo en aquellos lugares que se fundan inmediatamente después. Debido a la alta velocidad de refrigeración de tales puntos localmente calentados, la formación de grietas puede producirse en puntos de ignición que no se han solapado.
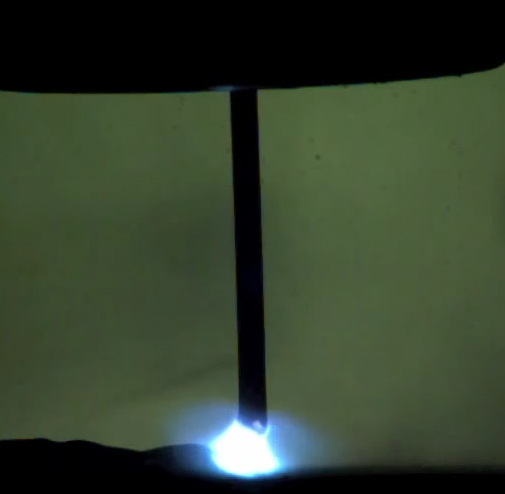
Guía de la antorcha
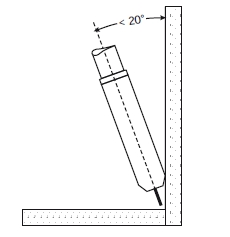
La antorcha se inclina en la dirección de soldadura entre 10° y 20° y puede dirigirse a derecha e izquierda. Su distancia con la pieza de trabajo debe ser tal que el stick-out, es decir, la distancia entre el borde inferior del tubo de contacto y el punto de inicio del arco voltaico, sea entre 10 y 12 veces el diámetro del hilo (mm). Si la antorcha de soldadura está demasiado inclinada, existe el riesgo de que entre aire en el gas de protección.
Suele utilizarse guía de la antorcha con penetración cuando se suelda con hilos macizos, mientras que en diagonal se emplea con hilos tubulares con formación de escoria. En la posición PG, la antorcha también se guía ligeramente en diagonal. La soldadura vertical descendente (Pos. PG) se utiliza principalmente con chapas más finas.
En las chapas más gruesas, existe el riesgo de que se produzca una falta de fusión por material de soldadura de avance. La falta de fusión causada por material de soldadura de avance se produce también si se suelda con velocidad de soldadura demasiado baja. Por consiguiente, salvo en la posición PF, deben evitarse movimientos oscilantes amplios. La forma habitual de oscilación es el triángulo abierto.
Finalización de la soldadura
Al final de la costura, el arco voltaico no debe apagarse repentinamente ni la antorcha retirarse del cráter final. Sobre todo con chapas más gruesas, donde pueden producirse cráteres finales profundos en pasadas de gran volumen, es mejor retirar el arco voltaico lentamente del baño o, si el sistema utilizado lo permite, ajustar un programa de cráter final. En la mayoría de sistemas, también se puede ajustar cierto tiempo post-gas del gas de protección, para que el último material de soldadura, aún líquido, pueda solidificarse bajo la cobertura del gas de protección. No obstante, esto solo es efectivo si la antorcha se mantiene durante un tiempo al final de la costura.
Parámetros de soldadura
El límite inferior para poder utilizar el proceso en soldaduras por aproximación en aceros sin alear es de unos 0,7 mm, en aceros inoxidables de 1 mm y en materiales de aluminio de unos 2 mm. Las pasadas de raíz y las chapas finas se sueldan normalmente con arco por cortocircuito o en el rango inferior de potencias del arco pulsado. Para capas de relleno, exteriores y opuestas de chapas más gruesas, se ajustará con arco voltaico largo de mayor potencia.
No obstante, estos trabajos de soldadura también pueden realizarse muy pobres en proyecciones con el arco pulsado. Los valores de corriente y de tensión que utiliza el soldador como información pueden leerse en la mayoría de instrumentos de medición que suelen ir incorporados en las máquinas. En la soldadura de arco pulsado, los instrumentos de visualización indican el valor medio aritmético que resulta de la corriente y la tensión de arco producida en la fase de pulso y base con la frecuencia de pulso ajustada.
Por consiguiente, las tablas también pueden utilizarse como valores de referencia para la soldadura MIG/MAG de arco pulsado. Si los aparatos no llevan instrumentos de medición, se pueden usar otros externos, o el soldador deberá orientarse por la velocidad del hilo indicada en las tablas. Además, establecerá la longitud de arco correcta de acuerdo con lo que ve y oye.
Para una buena soldadura MIG/MAG se necesita el siguiente equipamiento:
- Fuente de corriente de soldadura
- Antorcha
- Borne de la pieza de trabajo, pinza de masa
- Herramientas de soldadura
- Ropa de trabajo de seguridad
Encontrará más información sobre soldadura MIG/MAG en nuestro Glosario de soldadura.