Basi della saldatura TIG
- Da sapere sulla saldatura TIG
- Scelta del materiale d'apporto
- Impostazione della quantità di gas di protezione
- Pulizia della superficie del pezzo
- Accensione dell’arco
- Guida della torcia TIG
- Posizione di saldatura
- Parametri di saldatura
- Saldatura con impulsi di corrente
- Attrezzatura necessaria
Da sapere sulla saldatura TIG
La saldatura TIG è un processo di saldatura di impiego universale, per quanto riguarda i materiali da trattare, gli spessori delle pareti e le posizioni di saldatura. Permette infatti di realizzare delle giunzioni di saldatura di massima qualità. La saldatura TIG – secondo la norma DIN 1910 – parte 4 la denominazione completa di questo processo è saldatura a gas inerte con tungsteno – proviene dagli USA, dove divenne nota nel 1936 con il nome saldatura Argonarc. Il processo venne introdotto in Germania solo dopo la Seconda Guerra Mondiale. Nei paesi di lingua inglese il processo si chiama TIG, dalla parola "tungsteno". Rispetto ad altri processo di saldatura, la saldatura TIG è caratterizzata da tutta una serie di interessanti vantaggi. Ad es. è di impiego universale.
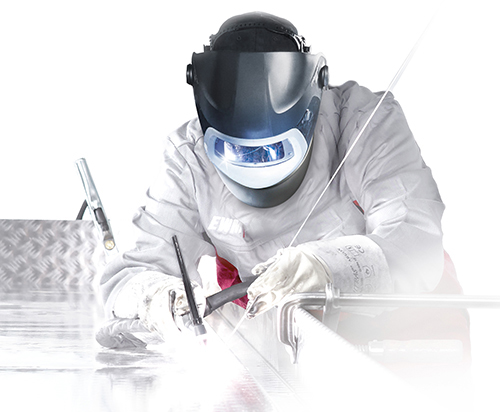
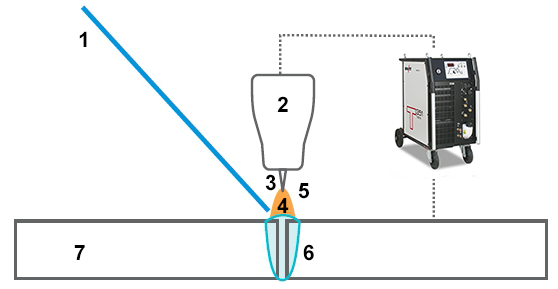
- Bacchetta di apporto
- Torcia
- Elettrodo di tungsteno
- arco
- Gas di protezione
- Bagno di fusione
- Materiale di base
Se un materiale metallico è adatto alla saldatura per fusione, allora può essere giuntato con questo processo. Si tratta di processo molto "pulito", che non genera quasi spruzzi e crea solo poche sostanze dannose; se applicato correttamente garantisce inoltre una giunzione di saldatura di alta qualità. Un particolare vantaggio della saldatura TIG rispetto ad altri processi che lavorano con la fusione dell'elettrodo è che in questo caso l'apporto di materiale d'apporto e il valore della corrente non sono accoppiati. Il saldatore può quindi impostare la corrente in modo ottimale per il lavoro di saldatura, apportando comunque il materiale d'apporto nella quantità al momento necessaria. Questo rende il processo particolarmente adatto alla saldatura di passate alla radice e alla saldatura in posizioni difficili. I vantaggi elencati hanno fatto sì che il processo TIG venga oggi impiegato con successo in molti settori dell'industria e dell'artigianato. In caso di applicazione manuale il processo richiede però al saldatore una mano abile e una buona formazione. La presente guida intende chiarire le particolarità del processo e magari risvegliare l'interesse di quelle aziende che ancora non lo utilizzano, pur occupandosi di lavori di saldatura idonei.
Scelta del materiale d'apporto
Nella saldatura TIG, il materiale d'apporto si presenta per lo più in forma di bacchette; nell'impiego interamente meccanizzato del processo viene invece apportato sotto forma di filo tramite un dispositivo separato. Di norma i materiali di apporto vengono scelti della stessa tipologia del materiale base. A volte, però, è necessario, per motivi metallurgici, che nel caso di alcuni elementi di lega il materiale d'apporto differisca un pochino dal materiale base. Questo ad esempio nel caso in cui sia presente un contenuto di carbonio, che viene mantenuto il più basso possibile per prevenire la formazione di cricche. In questi casi si parla di materiali d'apporto di tipologia analoga. Ci sono però alcuni casi che rendono necessario l'impiego di materiali di apporto di tipologia diversa. È il caso, ad esempio, della giunzione di acciai C di difficile saldatura, dove vengono utilizzati materiali di apporto austenitici oppure persino leghe a base nichel. Il diametro del materiale d'apporto deve essere adatto al lavoro di saldatura. Si orienta in base allo spessore del materiale e quindi anche in base al diametro dell'elettrodo di tungsteno. Le bacchette di apporto sono di norma lunghe 1000 mm. Vengono fornite a fasci e dovrebbero essere contrassegnate singolarmente con il contrassegno DIN o la denominazione commerciale, al fine di evitare scambi accidentali.
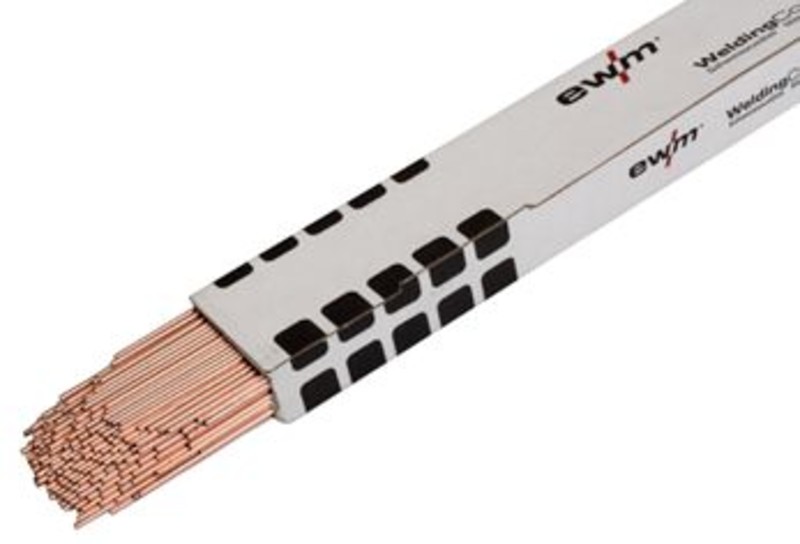
Impostazione della quantità di gas di protezione
La quantità di gas di protezione viene impostata come volume di flusso in l/min. Il valore dipende dalla dimensione del bagno di fusione e quindi anche dal diametro dell'elettrodo, dal diametro dell'ugello guidagas, dalla distanza tra l'ugello e la superficie del materiale base, dal flusso d'aria circostante, nonché dal tipo di gas di protezione - vedere paragrafo sui gas di protezione. Una semplice regola empirica dice utilizzando l'argon come gas di protezione unitamente a elettrodi di tungsteno dei diametri più comunemente utilizzati (da 1 a 4 mm) debbano venire apportati da 5 a 10 litri di gas di protezione ogni minuto. La misurazione della portata può avvenire indirettamente mediante manometri che misurano la pressione proporzionale alla portata presso un venturimetro integrato. In questo caso, la scala del manometro è tarata direttamente in l/min. Sono però più precisi gli strumenti che eseguono la misurazione, mediante tubicino in vetro e galleggiante, direttamente nel flusso di gas di protezione che scorre verso la torcia.
Pulizia della superficie del pezzo
Per un buon risultato di saldatura è importante pulire accuratamente, prima di iniziare la saldatura, le facce del giunto e la superficie del pezzo da lavorare attorno all'area di saldatura. Le superfici dovrebbero risultare di metallo lucido ed essere prive di grasso, sporco, ruggine o colori. Dovrebbero, se possibile, essere rimossi anche gli strati di scorie. In molti casi basta una spazzolata. Quando questa non è sufficiente, la superficie dovrà essere trattata con levigatura o con altro processo di lavorazione meccanico. In caso di materiali resistenti alla corrosione devono essere utilizzate esclusivamente spazzole in acciaio inossidabile, poiché altrimenti potrebbe venirsi a creare della ruggine dovuta a particelle di ferro esterne, che verrebbe poi inglobata nella superficie. Per via della formazione di pori, nel caso dell'alluminio è particolarmente importante che sulla superficie non rimangano spesse pellicole di ossido. Per la pulizia e lo sgrassaggio devono essere utilizzati solventi idonei. Attenzione: In caso di utilizzo di solvente contenenti cloro possono venirsi a creare vapori tossici.
Accensione dell’arco
L'arco non dovrebbe mai venire acceso al di fuori del giunto sul materiale base, bensì sempre in modo che il punto di accensione venga poi immediatamente fuso con la saldatura. All'inizio della saldatura il materiale base, riscaldato ad alta temperatura, si raffredda molto rapidamente presso il punto di fusione, a causa delle masse fredde posteriori che sottraggono calore. La conseguenza di questo rapido raffreddamento possono essere pori e indurimenti, eventualmente già connessi a cricche. Il raffreddamento rapido può essere evitato se l'accensione avviene direttamente all'inizio del cordone di saldatura, fondendo immediatamente le eventuali irregolarità che dovessero venirsi a creare. L'accensione a contatto dovrebbe essere un'eccezione, da utilizzare se il generatore di saldatura di vecchio stampo utilizzato non dispone di un ausilio per accensione (accensione a impulsi ad alta tensione). In questo caso l'accensione avviene su una piastrina di rame inserita nel giunto nella vicinanza dell'inizio del cordone di saldatura. Da lì l'arco viene quindi portato fino all'inizio del cordone previsto e la saldatura può avere inizio. In caso di accensione a contatto direttamente sul materiale base, è possibile che nel materiale di saldatura penetri del tungsteno, che per via dell'alto punto di fusione non viene fuso e che sarà poi riconoscibile nell'esposizione alle radiazioni come punto più chiaro, per via del maggiore assorbimento dei raggi X del tungsteno.
Guida della torcia TIG
(vedi illustrazione a destra)
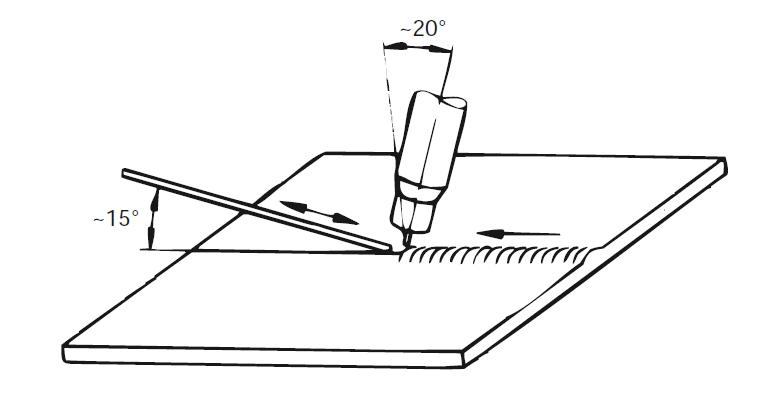
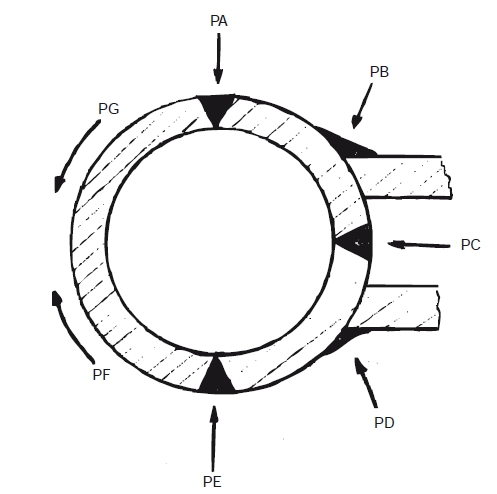
Posizione di saldatura
Secondo ISO 6947 le posizioni di saldatura vengono definite PA – PG. Se guardate applicate su un tubo, queste sono disposte a partire dall'alto (PA) in senso orario in ordine alfabetico. La posizione PA è quella che in Germania veniva precedentemente chiamata posizione orizzontale o posizione vasca. Seguono le posizioni di saldatura di testa PC (orizzontale su parete verticale) e PE (sopra la testa dell'operatore) nonché e posizioni di saldature d'angolo PB (orizzontale) e PD (orizzontale/sopra la testa dell'operatore). Nella saldatura di lamiere PF indica una saldatura verticale ascendente, mentre PG indica la saldatura verticale discendente. Se applicate al tubo, però, sotto queste sigle sono riassunte più posizioni. La posizione PF sussiste quando il tubo viene saldato partendo dalla posizione sopra la testa, senza rotazione, in senso ascendente da entrambi i lati; nella posizione PG questo vale per la saldatura dall'alto verso il basso (saldatura verticale discendente). La saldatura TIG è possibile in tutte le posizioni. I dati di saldatura devono essere regolati in base alla posizione, come avviene anche per altri processi di saldatura.
Parametri di saldatura
Il limite inferiore di applicabilità del processo TIG è, per l'acciaio, pari a circa 0,3 mm, per l'alluminio e il rame pari a 0,5 mm. Per quanto riguarda i limiti superiori, questi sono, se il caso, solo limiti economici. La velocità di fusione del processo non è molto elevata. Spesso vengono quindi saldate col processo TIG solo le passate alla radice, mentre le altre passate vengono eseguite con altri processi (E, MAG) che hanno una velocità maggiore. Nella scelta dei parametri di saldatura occorre rammentare che sul generatore di saldatura viene impostato solo il valore della corrente, mentre la tensione dell'arco risulta dalla lunghezza dell'arco che mantiene il saldatore. La tensione diventa maggiore tanto più aumenta la lunghezza dell'arco. Il valore di riferimento per un valore della corrente sufficiente per la saldatura dell'acciaio con una passata unica in corrente continua (polo negativo) è pari a 45 ampere per ogni mm di spessore della parete. Per la saldatura di alluminio in corrente alternata sono necessari 40 ampere/mm.
Saldatura con impulsi di corrente
Nella saldatura con corrente a impulsi, il valore della corrente e la tensione passano costantemente da un valore di base più basso a un valore di impulso più alto, commutando allo stesso ritmo della frequenza degli impulsi. Sotto l'effetto della più elevata corrente a impulsi si genera la penetrazione nel materiale base e si forma così un bagno di fusione puntiforme. Questo inizia a indurirsi, a partire dai margini, sotto l'influsso della successiva corrente di base, di valore inferiore, fino a che il successivo impulso di corrente lo fonde nuovamente e lo ingrandisce. Nel frattempo, però, l'arco è però già passato oltre alla velocità di saldatura, cosicché il cordone di saldatura, nella saldatura TIG a impulsi, risulta formato da numerosi punti di saldatura sovrapposti. La dimensione del bagno di fusione è in media inferiore a quella della saldatura con corrente continua, cosa che lo rende più gestibile in posizioni difficili. Nonostante questo è comunque garantita una penetrazione sufficiente. L'effetto appena descritto si verifica però solamente se nel bagno di fusione è presente una sufficiente differenza di temperatura tra fase di base e fase di impulso. Questa condizione si verifica solo con frequenze di impulso inferiori a circa 5 Hz. Uno svantaggio consiste nella necessità di ridurre spesso la velocità di saldatura durante la saldatura a impulsi. Inoltre il saldatore percepisce gli impulsi nel range di frequenza inferiore come fastidioso sfarfallio dell'arco. Per questo motivo, questa variante della saldatura TIG viene impiegata più raramente nella saldatura manuale, dove il saldatore ha altre possibilità per influire sulla gestione del bagno di fusione, e più frequentemente nella saldatura TIG meccanizzata.
Per un'efficiente saldatura TIG è necessaria la seguente attrezzatura:
- Fonte della corrente di saldatura
- Torcia
- Morsetto per pezzo da lavorare/pinza di massa
- Elettrodo rivestito
- Attrezzi di saldatura
- Abbigliamento protettivo da lavoro
Ulteriori informazioni sulla saldatura TIG sono riportate nel nostro Glossario della saldatura.